Cамостоятельная сборка рамы настольного ЧПУ станка 2418 или Наши руки не для скуки, часть вторая
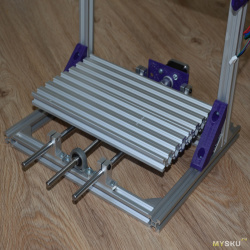
- Цена: В тексте есть калькуляция затрат для самостоятельной сборки CNC2418
- Перейти в магазин
Продолжаю предыдущий обзор на тему постройки станка CNC2418 из алюминиевого профиля своими руками.
Будет краткая инструкция по сборке рамы и примерная калькуляция затрат
Обещал — продолжаю. Материала много, стараюсь подготовить и опубликовать все в сжатые сроки. Прошлый раз я описал комплектующие для сборки настольных ЧПУ станков наподобие CNC1610 или CNC2418.
Часть первая: комплектующие
Часть вторая: сборка рамы
Часть третья: сборка оси Y и рабочего стола
Часть четвертая: электроника станка
Внешний вид популярного станка CNC2418
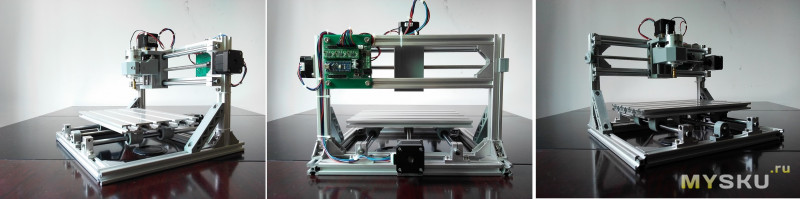
И несколько слов про станочек CNC2418
Как правило, продается в районе $250 (от $170 до $300) в разной комплектации. Есть версия с разными шпинделями (различные вариации 775го двигателя), с разными цангами (от простой для сверл до ER11), может комплектоваться лазерным модулем. Обычно продавцы вкладывают расходники, биты-фрезы и прочее.
Характеристики станка 2418:
Электроника типа Atmega+CNC Shield, EleckMill, или оригинальные платы, но с прошивкой GRBL. Управляются с помощью GrblController, UniversalGcodeSender, grblControl, используют файлы *.nc. Генерировать подобные файлы нужно отдельно.
Размеры рамы и расположение осей CNC 2418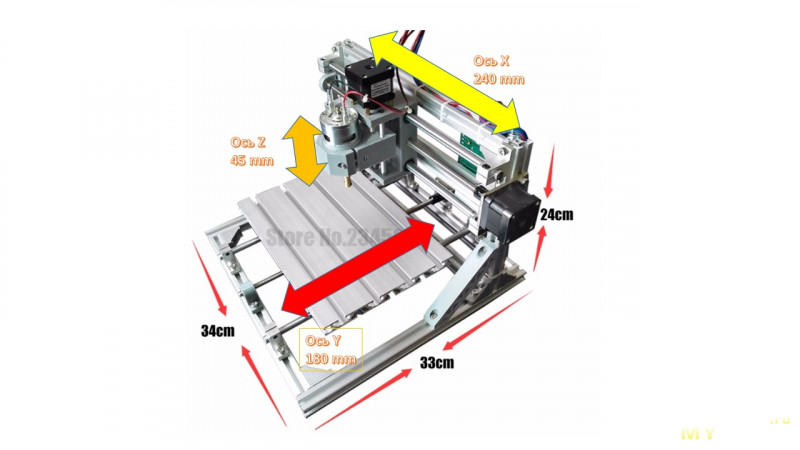
Варианты цангового зажима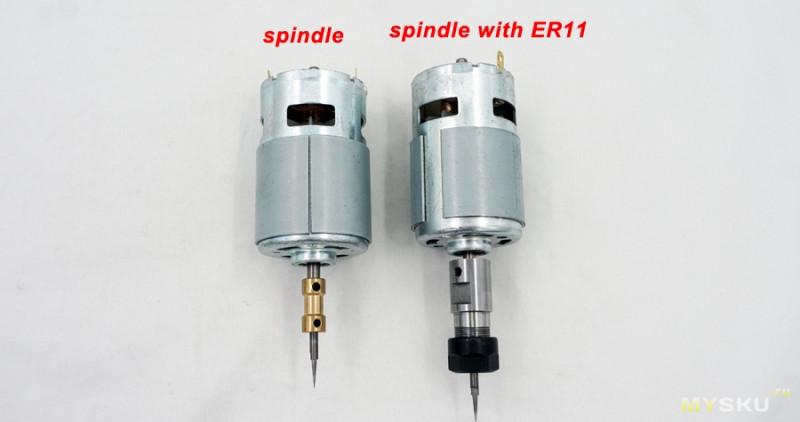
В составе оригинального станка 2418 (как впрочем и аналогичного 1610) присутствуют 3Д печатные составные части.
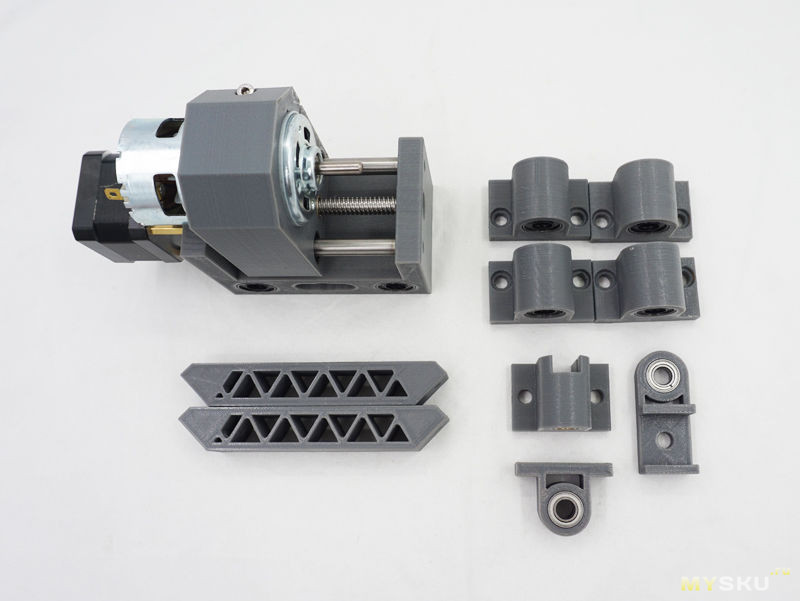
Использование подобных пластиковых деталей хорошо видно на пользовательских фотографиях из интернета, да и в лотах у продавцов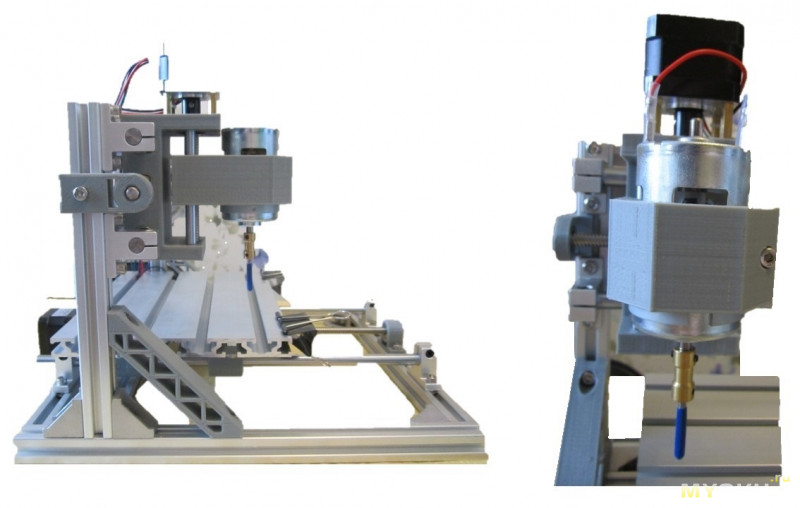
В печатный комплект входит распорка-уголок (2 шт), держатель винта Х, держатель винта Y, держатели подшипников LM8UU (а скорее их имитации) 4 шт, держатель гайки Т8.
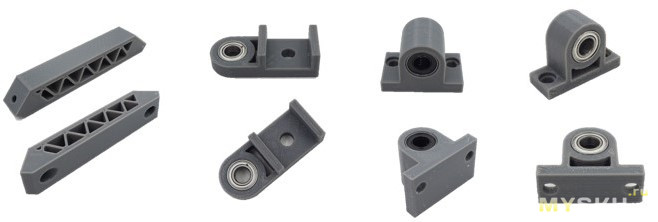
Отдельно выделю сборку держателя шпинделя, одновременно каретку по XY.
Она так и приходит в сборе с установленным двигателем.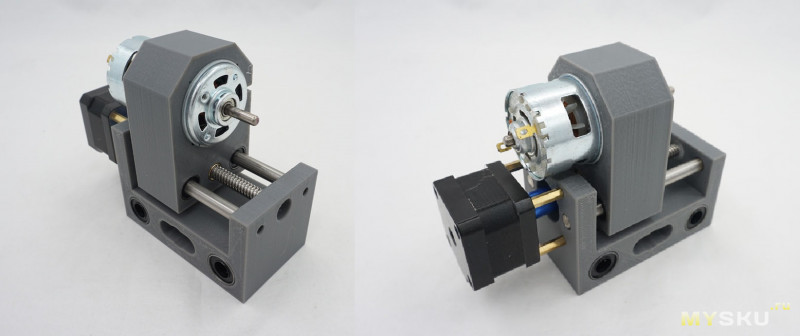
Модель подобного крепления для шпинделя
Теперь чуть более подробнее по основную сборку.
Итак, для сборки рамы потребуются следующие комплектующие:
Итак, начинаем собирать раму настольного станка 2418.
Вот уже порезанный профиль.
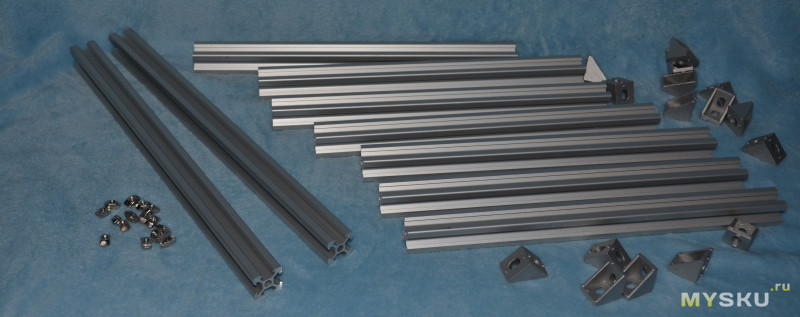
В данной конструкции я увеличил ось Z (чуть больше на пару см чем другие), чтобы использовать станок как ЧПУ сверлилку.
В оригинале ось Z самая короткая. Это уже решаете вы под свои цели. Чтобы удлинить рабочее поле, нужно купить два отрезка профиля (продольная пара) больше на нужную длину (например, +10 см), соответственно удлиняются направляющие (+10 см паре 8мм валов) и винт (+10 см винту Т8). По деньгам выходит совсем дешево озвученные +10 см: стоимость 10+10 см профиля около 40р, направляющие и винт обойдутся в плюс $6 (проверить).
Вот подготовленные для сборки уголки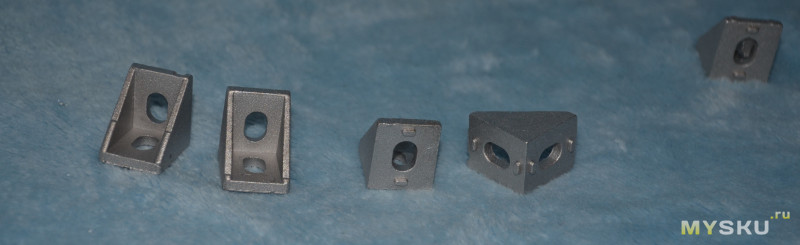
Вот таким образом следует устанавливать Т-гайки в слот. Можно не продевать с торца, а устанавливать прямо в паз профиля боком, но потом контролируйте поворот и установку гайки, так как не всегда это происходит, нужна некоторая сноровка.
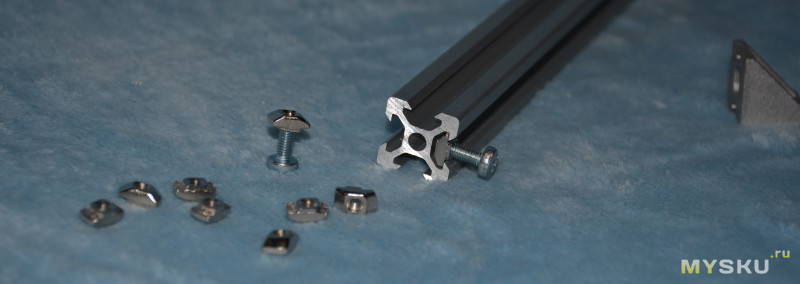
Рез профиля чистый, заусенцев нет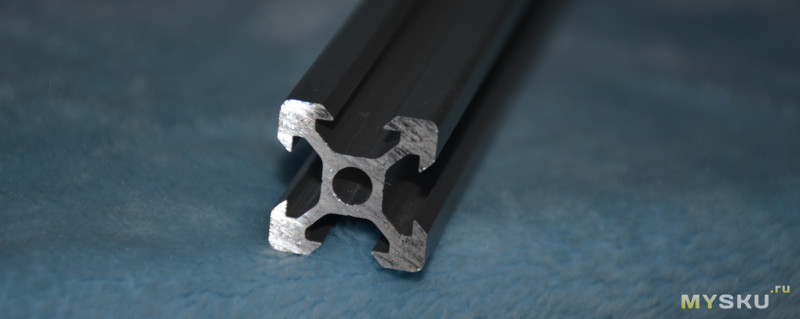
Профиль-двадцатка, то есть из серии 2020, с соответственно разменами 20мм х 20 мм, паз 6 мм.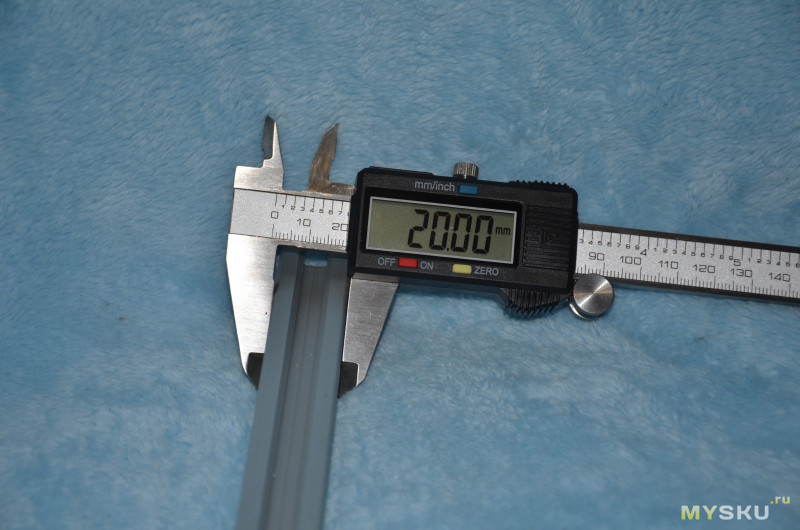
Итак, сначала собираем П образную часть рамы, крепим две продольных части профиля и одну крайнюю поперечину. Большого значения с какой стороны собирать нет, но учитывайте, что есть центральная поперечная перекладина, которая сдвинута ближе к задней части. Она является частью вертикальной плоскости, а размер смещения зависит от вылета оси Z и шпинделя. Размещают таким образом, чтобы ось вращения шпинделя была по центру станка (оси Y).
Далее собираем среднюю поперечину. Удобнее сначала установить оба уголка на отрезок профиля и зафиксировать, а затем устанавливать к раме.
Прикладываем отрезок профиля, вымеряем одинаковое расстояние линейкой, затягиваем винты. Винты нужно затягивать неторопливо, давать время Т-гайке провернуться и занять свое положение в пазу. Если не получается с первого раза, опять ослабить гайку и повторить.
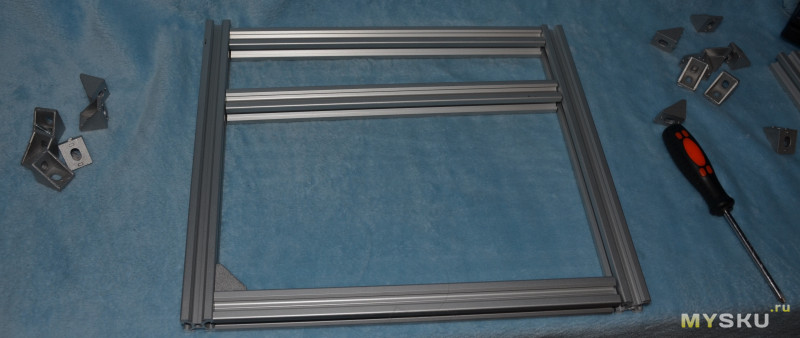
Устанавливаем последнюю часть горизонтальной рамы. Удобнее подлезать длинной отверткой. Не поленитесь и проконтролируйте прямые углы полученной конструкции угольником и диагонали — линейкой.
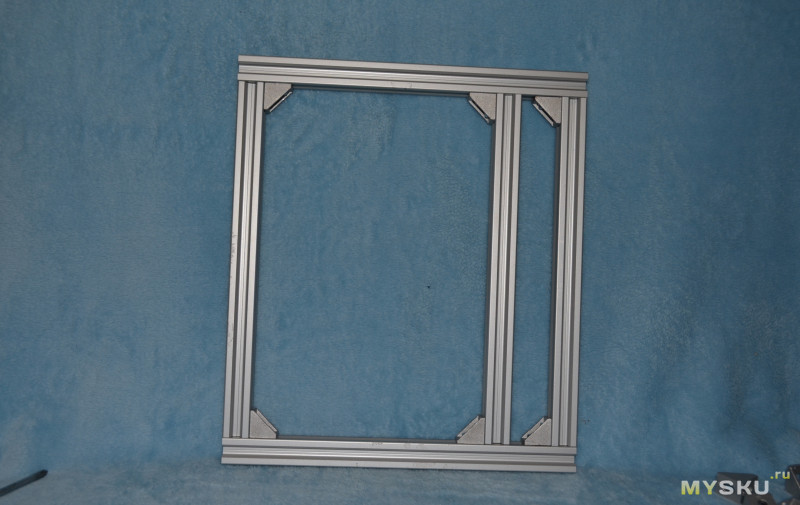
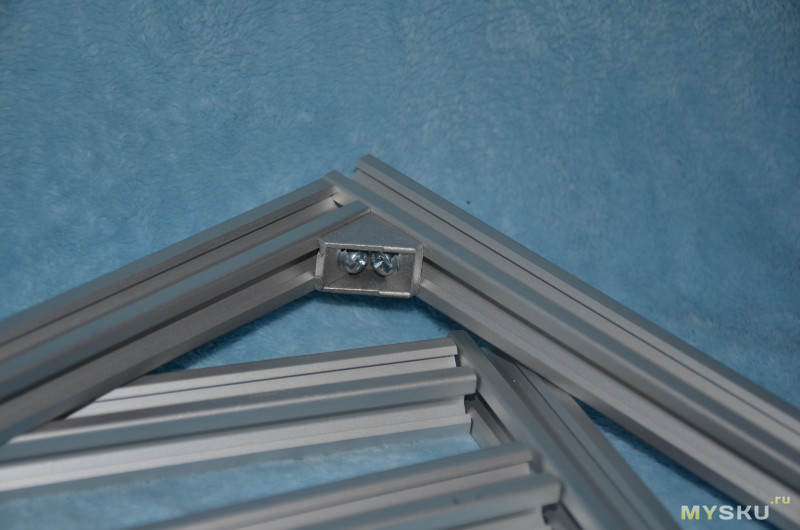
Так как уголки конструкции направлены друг к другу, то не принципиально в каком порядке собирать. Я сделал как в базовой конструкции CNC2418. Но интуиция подсказывает, что расстояние между профилями имеет смысл увеличить, особенно при большей высоте портала. Ну ладно, это можно будет сделать позже.
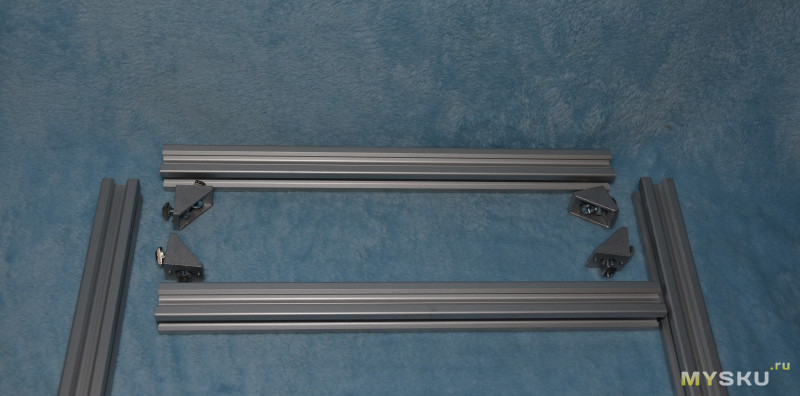
Далее начинаем собирать крепление вертикального портала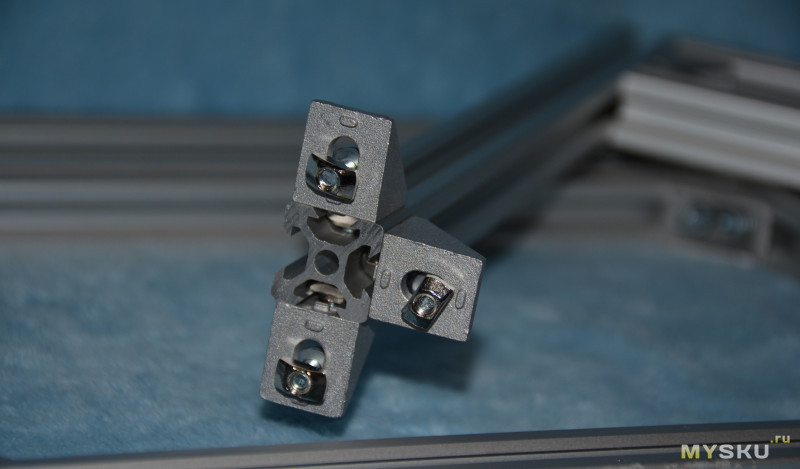
Собранный портал устанавливаем на горизонтальную часть, крепим с помощью 6 уголков (устанавливаются по направлению в три стороны от вертикального профиля).
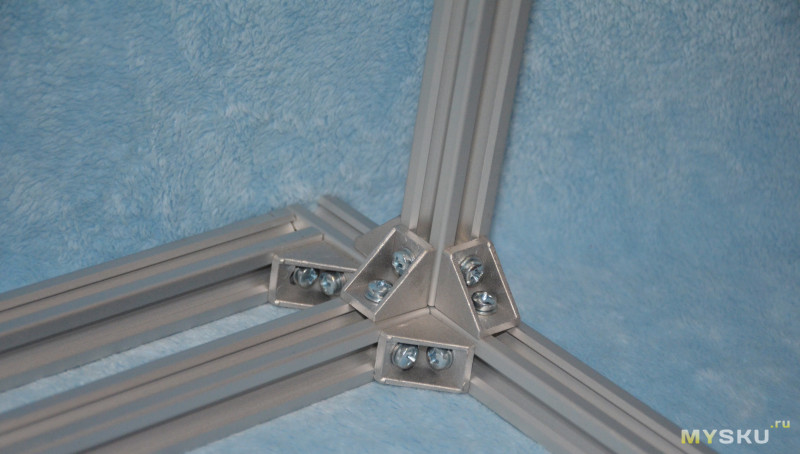
Устанавливаем, соблюдаем перпедникулярность отрезков (по угольнику). Затем по очереди затянул все винты.
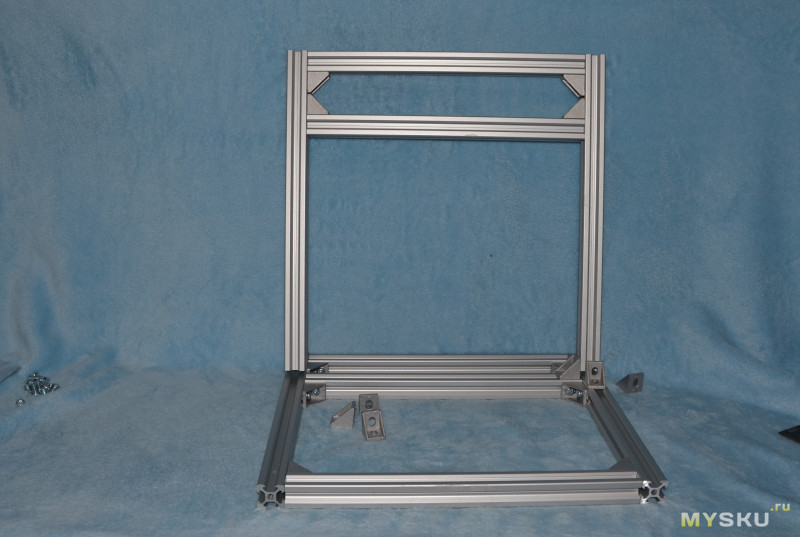
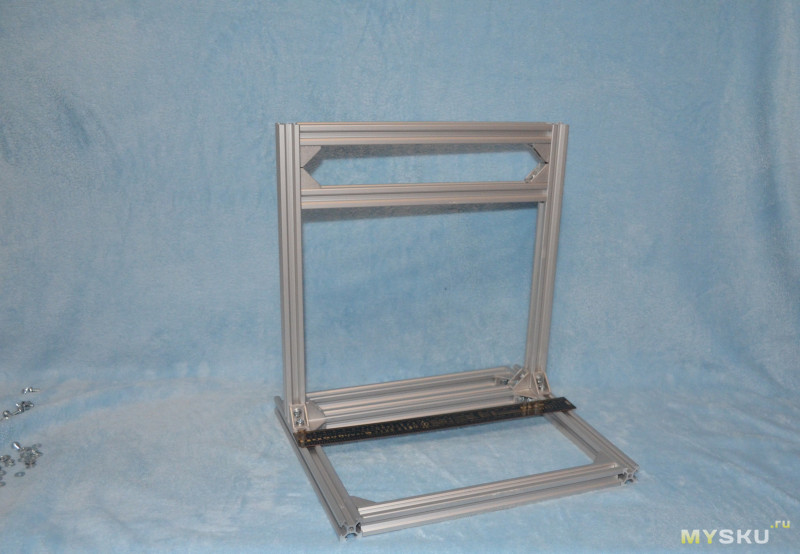
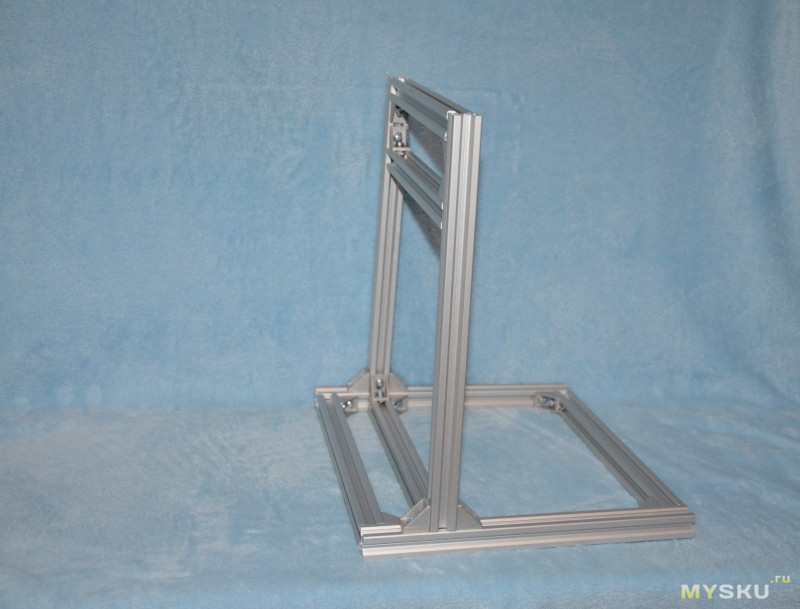
В оригинале для укрепления вертикали используется особый экструзионный уголок под 45°. Я подобный не смог найти в продаже, заменил 3Д-печатным. Ссылка на модель есть в конце топика.
Update: оказалось в оригинале 3Д печатный тоже.
Если что заменить его можно перфорированным крепежом из магазинов, либо мебельными уголками. На качестве это никак не скажется.
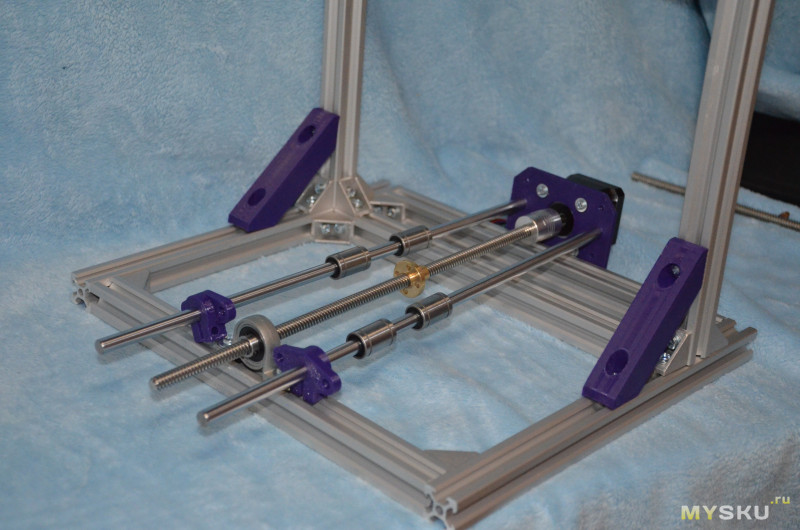
Конструкция получилась на первый взгляд прочная, не шаткая. Видно, что пластина с двигателем короче, чем связка суппортов KP08+SK8. Буду разносить пошире.
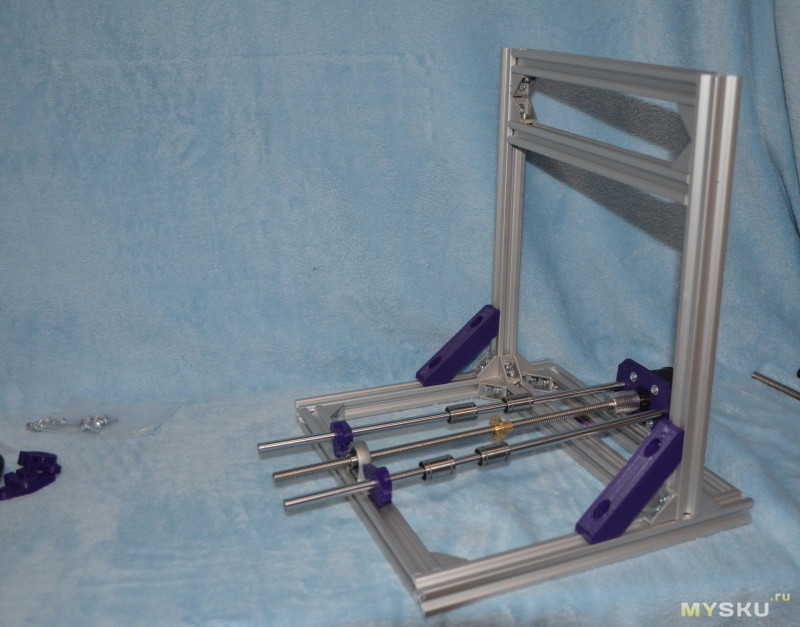
По сути данная рама является копией подобной конструкции станка CNC2418, разве что я прямо не копировал размеры, сделал чуть побольше для того, чтобы меньше обрезков от направляющих и винтов.
Сборка рамы закончена, теперь можно заняться установкой двигателей. Я использовать 3Д печатные фланцы для установки двигателей. Верхние целесообразно сделать в сборе с держателями направляющих, нижние — без держателей, так как ось Y должна быть шире. Ось Y целесообразно установить на суппорты SK8 и KP08, как в оригинальном станке. Сами суппорты можно распечатать на принтере либо купить (ссылки в конце топика, а также были в первом посте).
Для одной из осей (оси X и Y у меня одинаковой длины) взял «пристрелочный» комплект двигатель Nema17 плюс винт и суппорты. Я еще не знал своих «хотелок» на размеры станка. В итоге обрезки от винта пойдут на ось Z, нужно будет только докупить латунную гайку Т8.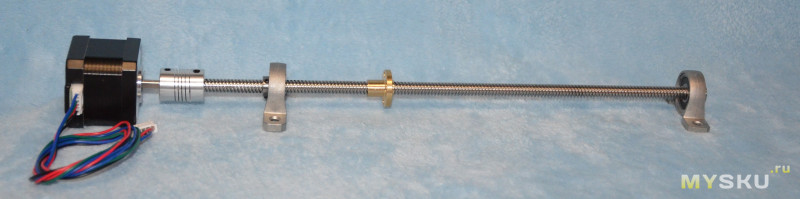
Упакован был в картонную упаковку, внутри каждая деталь в пакете отдельно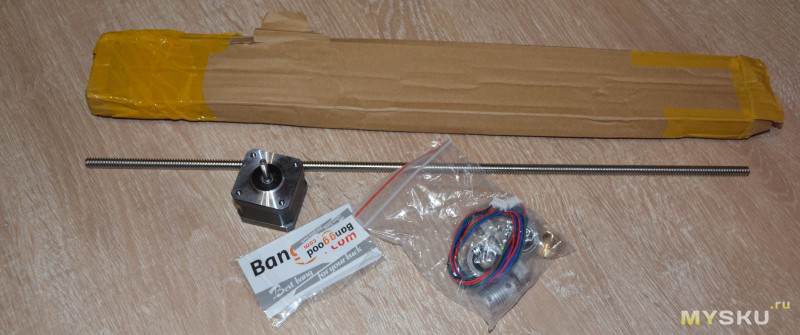
Выглядит комплект вот таким образом: двигатель с коротким проводом, ходовой винт Т8, два суппорта KP08 и две муфты 5х8.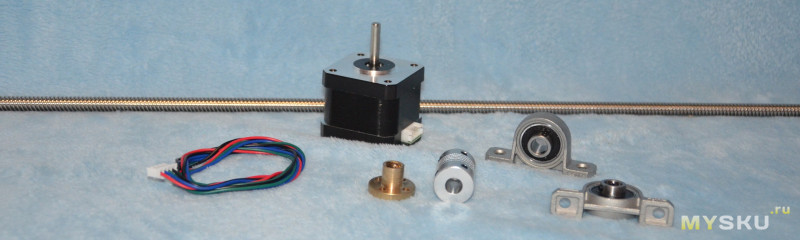
Есть аналогичный комплект 400 мм и 300 мм, а также без двигателя на 600 мм (с суппортами и гайкой).
Если брать без большого запаса, то вариант на 400 мм, хорошо пойдет для «увеличенной версии» станка
Вот как крепится двигатель в оригинале на ось Х. На небольшую алюминиевую пластину.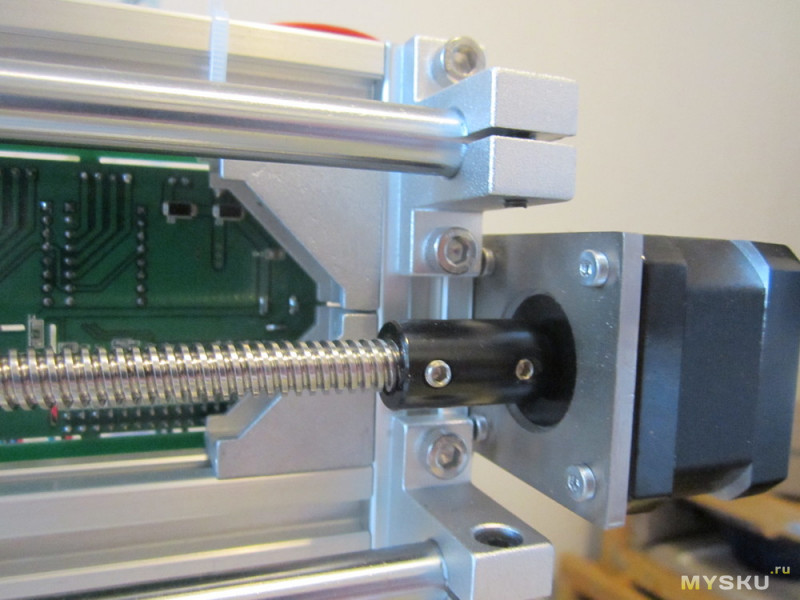
Сделал тоже самое, только с печатной пластиной. Заодно будет суппортом для направляющих.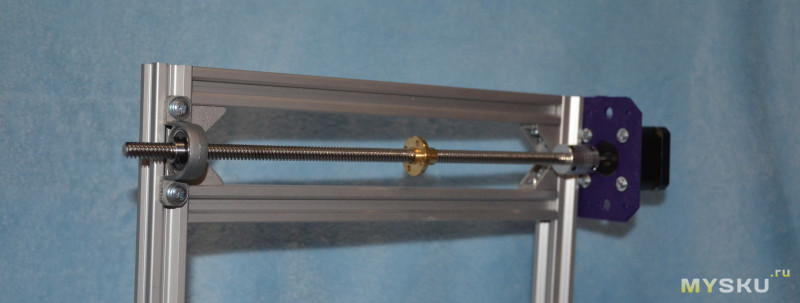
Лишнюю длину винта уже отрезал для оси Z (ось Z в процессе пока, информация будет отдельно, скорее всего также 3д печатная).
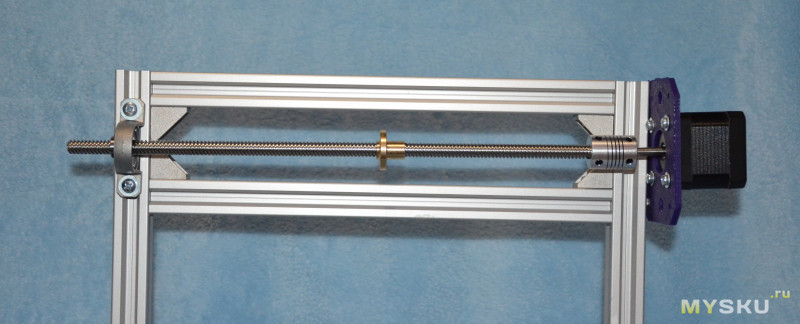
С большой вероятностью нужно будет удлинить провода двигателей, чтобы аккуратно проложить его по профилю в верхнюю часть до платы электроники (скорее всего будет CNC Shield). Да и не мешало бы установить концевики крайних положений.
Основная информация по сборке уже есть, можно приступать к оценке затрат))))
Калькуляция
Теперь, по просьбам в комментариях в первой части, я предлагаю обсудить калькуляцию затрат. Естественно, я потратил меньше указанного, так как двигатели и большая часть комплектующих у меня была в наличии. Сильно дешевле будет, если использовать самодельные печатные уголки для профиля, суппорты, фланцы и так далее. На работу станка по сверлению печатных плат и по фрезеровке мягких материалов это вряд ли скажется. Еще хороший вариант — использование перфорированных пластин из строительных/хозмагов. Пойдет для усиления углов, в том числе вертикального и для установки двигателя, при условии высверливания центральной части под вал. В место перфорированного крепежа можно использовать самодельные из алюминиевого листа или фанеры.
Однозначно нужно приобретать профиль 2020, иначе это будет станок совершенно другого типа. Можно сделать тоже самое из алюминиевого уголка или прямоугольной трубы, но только из любви к искусству))) Есть более оптимальные конструции в плане жесткости для сборки из уголка/трубы.
Однозначно к профилю нужны Т-гайки. Можно купить Т-болты, но Т-гайки более универсальные (так как длину винта можно применить любую).
А вот остальное можно менять на свое усмотрение, можно даже вместо ходового винта Т8 использовать шпильку из нержавейки. Разве что количество шагов на мм пересчитать придется в прошивке.
Двигатели можно снять со старых устройств/оргтехники и планировать посадочные места уже под конкретный тип.
Электроника практически любая (Anduino UNO/Anduino Nano, CNCShield, Mega R3+Ramps, драйверы A4988/DRV8825, можно использовать плату-переходник под Mach3 и драйверы TB6600. Но выбор электроники ограничивает используемый софт.
Для сверлилки можно использовать любой двигатель постоянного тока, который позволяет установить цанговый патрон и имеет приличные обороты. В базовом варианте присутствует высокооборотистый двигатель 775. Для фрезеровки можно использовать б/к шпиндели ватт на 300 с цангой ER11, но это сильно удорожает станок в целом.
Примерная калькуляция затрат:
профиль Соберизавод 2020 (2,5 метра) = 667р
профиль Соберизавод 2080 (0,5 метра) на рабочий стол = 485 р
Два комплекта для осей по 300 мм 2х$25
Уголки для профиля 16 шт. Лот на 20 шт выходит $5.5 с доставкой
Т-гайки примерно 4р/штука если брать большой пакет. Нужно не менее 50 шт (крепление двигателей, суппортов). Винты к ним не считаю, обычно несколько копеек/штука в зависимости от качества. Итого около 400...500р.
Двигатели Nema17 3 шт $8.25 каждый
Электроника CNC Shield board $2
Arduino Uno $3.5
A4988 три штуки по $1
Станок выходит около $111. Если добавить шпиндель:
Двигатель 775 $9
Патрон ER11 $7.78,
то итог стоимости около $128
3Д печатные детали не оцениваю. Можно заменить перфорированными пластинами/уголками из крепмаркета и подобных магазинов. Провода, изоленту, затраченное время также не оцениваю.
Напомню, что не во всех вариантах комплектаций CNC2418 есть такие хорошие 775 двигатели и, тем более, цанга ER11.
Варианты подешевле:
Вал 8х600 пару шт и распилить пополам. Для Z-оси взять короткий 8х300
Вместо SC8UU использовать LM8UU
Суппорты SK8, KP08, держатели Т8 гайки, держатели подшипников LM8UU, уголки для профиля — 3д печатные.
Можно взять направляющие большей длины, чем в Китае, например в магазине Duxe.ru. Как вариант, можно купить Вал полированный SFC-8/600 и SFC-8/1000. Цена вопроса 250 р и 410 р соответственно (плюс доставка). Из этого получится три пары направляющих с большим запасом.
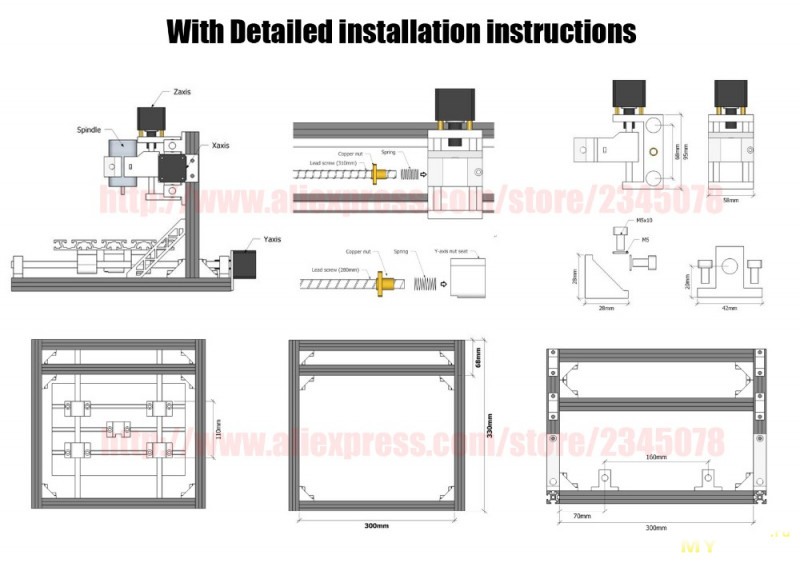
3D печатные запчасти, для экономии:
Целиком проект CNC с печатными деталями. Рекомендую воспользоваться моделью кареток XY отсюда
Модель крепления для шпинделя
Похожий зажим от CNC3020
Хорошее крепление пары LM8UU
Простой держатель LM8UU и еще один
Подшипники lm8uu можно также распечатать из PLA
Nema 17 motor mount — крепление мотора
Суппорт 8 мм c подшипником
SK8 mount
SHF8
Усиленный уголок для профиля
Еще несколько деталей, в том числе фланцы и уголок под 45°
Спасибо за ваше внимание. Далее будет про сборку осей XY и электронику
Будет краткая инструкция по сборке рамы и примерная калькуляция затрат
Обещал — продолжаю. Материала много, стараюсь подготовить и опубликовать все в сжатые сроки. Прошлый раз я описал комплектующие для сборки настольных ЧПУ станков наподобие CNC1610 или CNC2418.
Часть первая: комплектующие
Часть вторая: сборка рамы
Часть третья: сборка оси Y и рабочего стола
Часть четвертая: электроника станка
Внешний вид популярного станка CNC2418
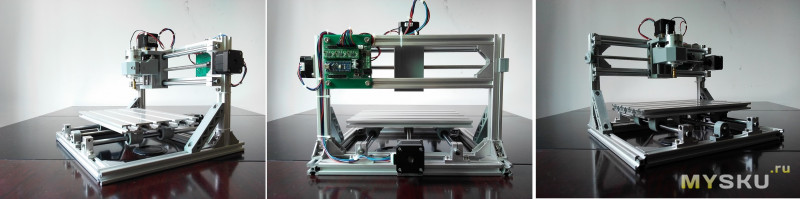
И несколько слов про станочек CNC2418
Как правило, продается в районе $250 (от $170 до $300) в разной комплектации. Есть версия с разными шпинделями (различные вариации 775го двигателя), с разными цангами (от простой для сверл до ER11), может комплектоваться лазерным модулем. Обычно продавцы вкладывают расходники, биты-фрезы и прочее.
Характеристики станка 2418:
- Рабочее поле — 240 мм х 180 мм х45 мм
- Размер рамы (станины) — 260 мм х180 мм (алюминиевый профиль)
- Общий размер — 330х340х240
- Шаговые моторы: 3шт Nema17 1,3А 0,25Nm
- Шпиндель: Диаметр 45мм, модель 775, 24V: 7000 r/min
- Максимальный диаметр хвостовика фрезы зависит от установленной цанги
- Питание: 24V 5.6A
Электроника типа Atmega+CNC Shield, EleckMill, или оригинальные платы, но с прошивкой GRBL. Управляются с помощью GrblController, UniversalGcodeSender, grblControl, используют файлы *.nc. Генерировать подобные файлы нужно отдельно.
Размеры рамы и расположение осей CNC 2418
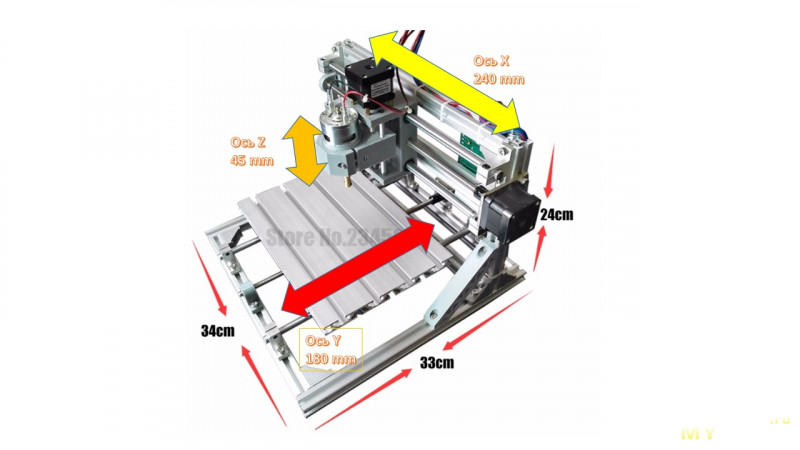
Варианты цангового зажима
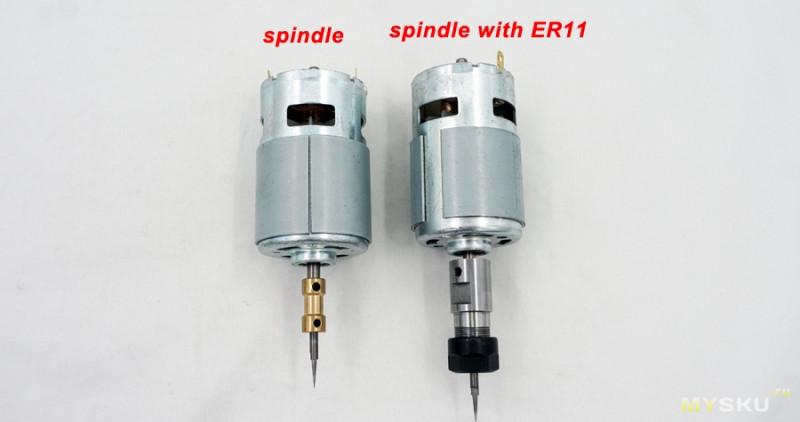
В составе оригинального станка 2418 (как впрочем и аналогичного 1610) присутствуют 3Д печатные составные части.
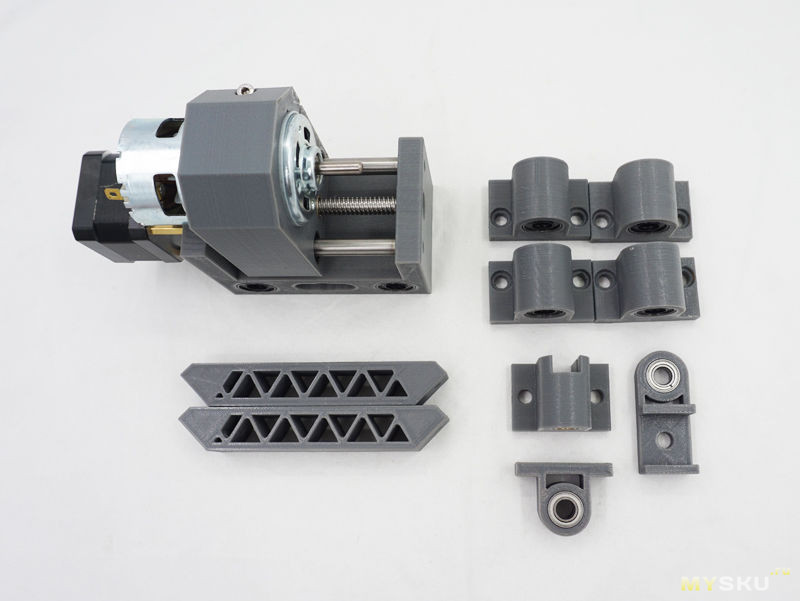
Использование подобных пластиковых деталей хорошо видно на пользовательских фотографиях из интернета, да и в лотах у продавцов
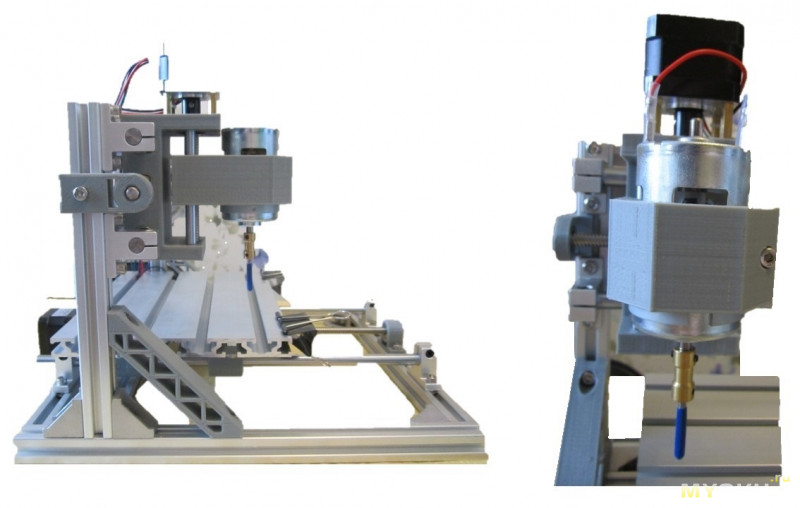
В печатный комплект входит распорка-уголок (2 шт), держатель винта Х, держатель винта Y, держатели подшипников LM8UU (а скорее их имитации) 4 шт, держатель гайки Т8.
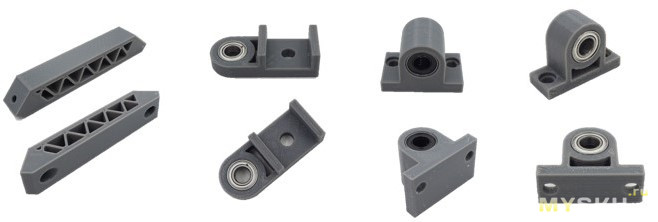
Отдельно выделю сборку держателя шпинделя, одновременно каретку по XY.
Она так и приходит в сборе с установленным двигателем.
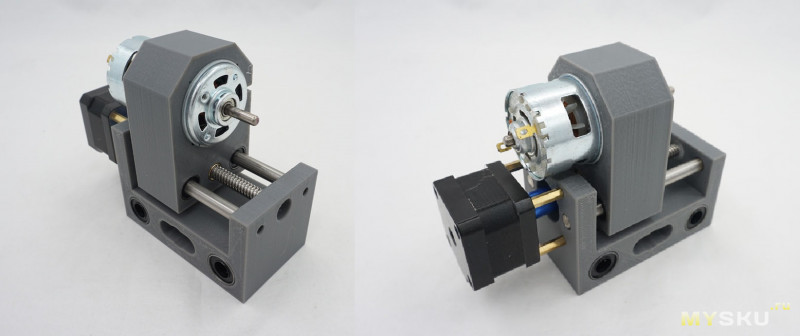
Модель подобного крепления для шпинделя
Теперь чуть более подробнее по основную сборку.
Итак, для сборки рамы потребуются следующие комплектующие:
- Отрезки профиля 2020 (две продольных, 5 поперечных, 2 вертикальных части)
- Уголки для профиля 16 шт
- Т-гайки М3 или М4 для паза-6мм
- Винты для установки с Т-гайками (М3 или М4 соответственно, на 8...10 мм, плюс М3х12 для крепления двигателей)
- Распорка (уголок под 45°)
- Инструмент (отвертка)
Раз завел разговор про профиль, то на всякий случай дублирую про закупку и нарезку профиля у Соберизавода
Это конструкционный алюминиевый профиль от Соберизавода.
Я покупал сразу нарезанный в размер комплект профиля для 2418.
Есть два варианта — профиль без покрытия (подешевле) и с покрытием (анодированный). Разница в стоимости небольшая, я рекомендую с покрытием, особенно если использовать в качестве направляющих для роликов.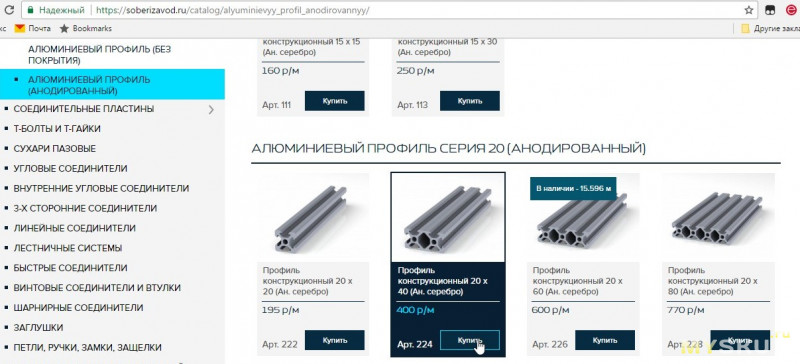
Выбираем нужный тип профиля 2020, далее вводим «порезать по размерам». Иначе, можно купить один отрезок (хлыст) на 4 метра. При расчете имейте ввиду, что стоимость одного реза бывает разная, в зависимости от профиля. И что на рез закладывается 4 мм.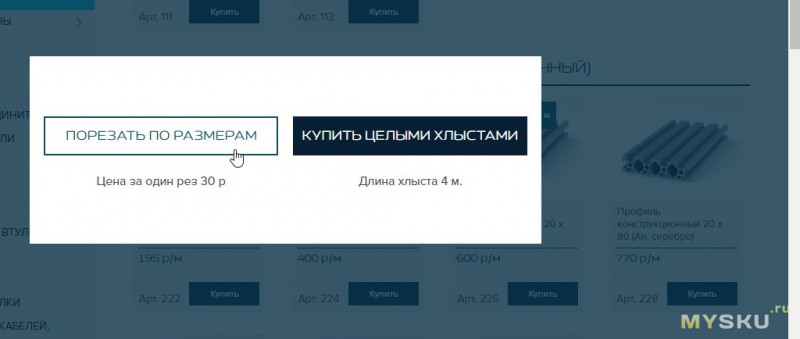
Вводите размеры отрезков. Я сделал станок 2418 чуть больше, это семь отрезков по 260 мм и два вертикальных по 300 мм. Вертикальный можно сделать поменьше. Если нужен станок длиннее, то два продольных отрезка больше, например, 350 мм, поперечные также по 260 мм (5 шт).
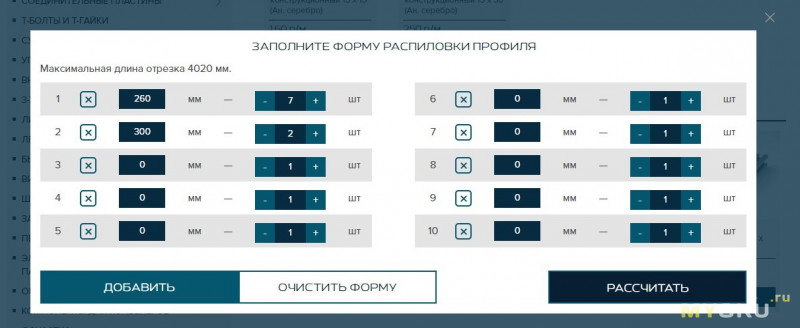
Подтверждаем (надо обязательно добавить в карту раскроя)
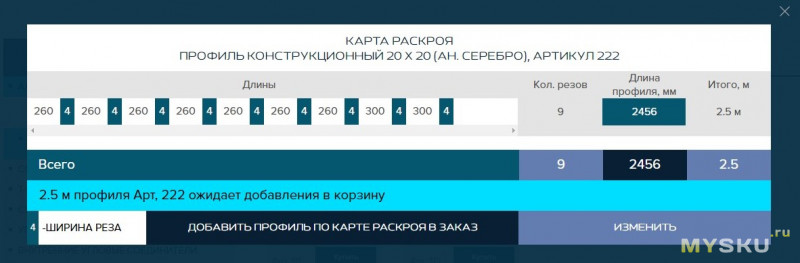
Проверяем корзину
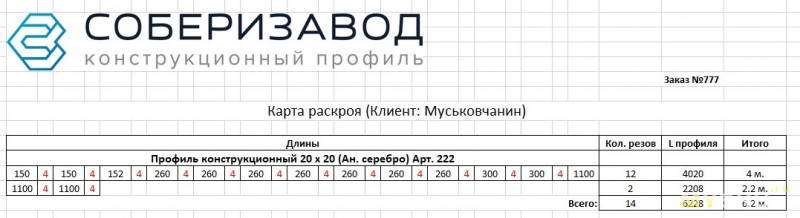
Профиль получается на 667р вместе с услугой резки.
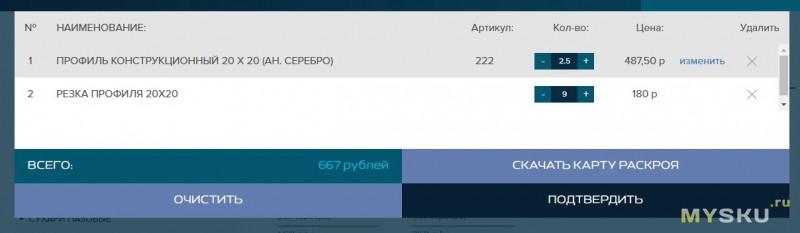
Доставка осуществляется ТК, рассчитать стоимость можно по калькулятору, так как размеры профиля вам известны, вес очень хорошо считается в карте раскроя. Для расчета нужна опция «забор груза у поставщика». Доставка Деловыми линиями обойдется дешевле, около 1000 рублей.
Можно забрать самовывозом в Москве.
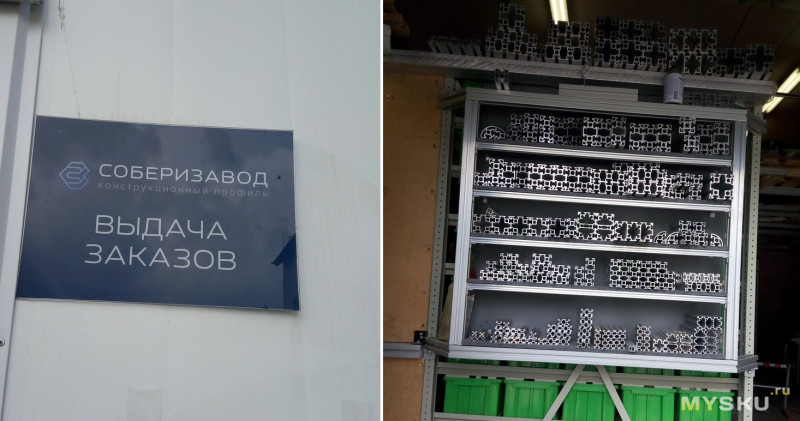
В одном месте офис, склад и мастерская, где режут профиль в размер. Есть витрина с образцами, можно подобрать профиль на месте.
Я покупал сразу нарезанный в размер комплект профиля для 2418.
Есть два варианта — профиль без покрытия (подешевле) и с покрытием (анодированный). Разница в стоимости небольшая, я рекомендую с покрытием, особенно если использовать в качестве направляющих для роликов.
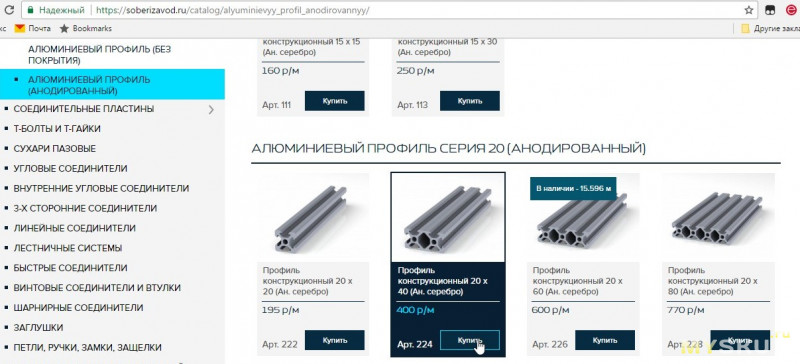
Выбираем нужный тип профиля 2020, далее вводим «порезать по размерам». Иначе, можно купить один отрезок (хлыст) на 4 метра. При расчете имейте ввиду, что стоимость одного реза бывает разная, в зависимости от профиля. И что на рез закладывается 4 мм.
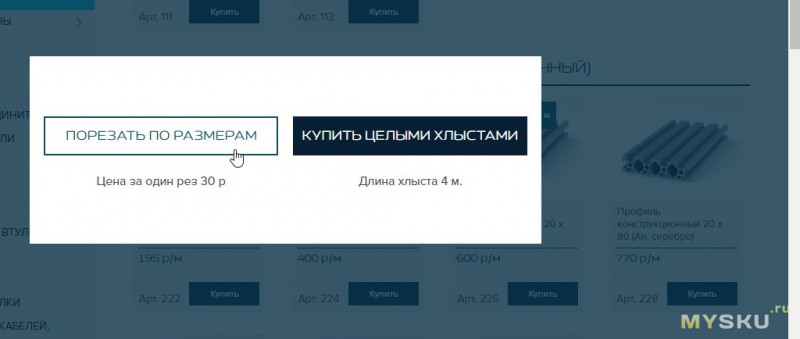
Вводите размеры отрезков. Я сделал станок 2418 чуть больше, это семь отрезков по 260 мм и два вертикальных по 300 мм. Вертикальный можно сделать поменьше. Если нужен станок длиннее, то два продольных отрезка больше, например, 350 мм, поперечные также по 260 мм (5 шт).
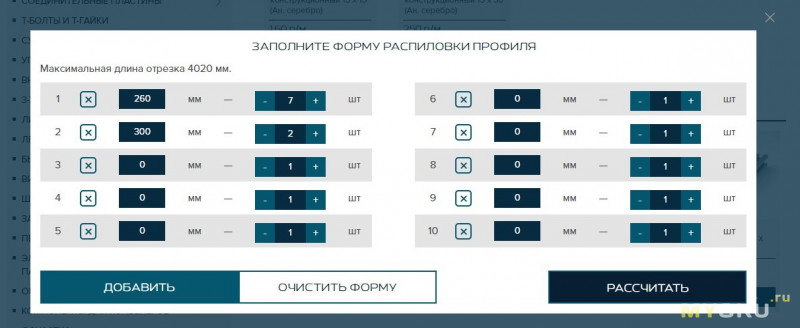
Подтверждаем (надо обязательно добавить в карту раскроя)
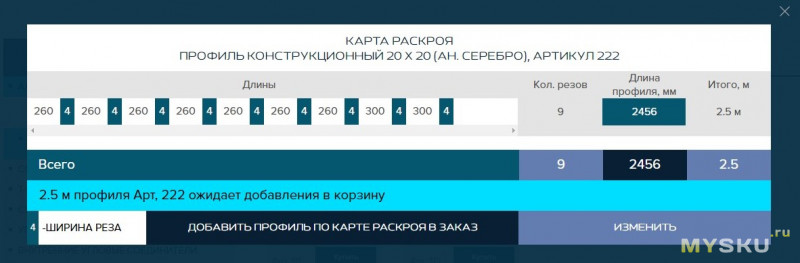
Проверяем корзину
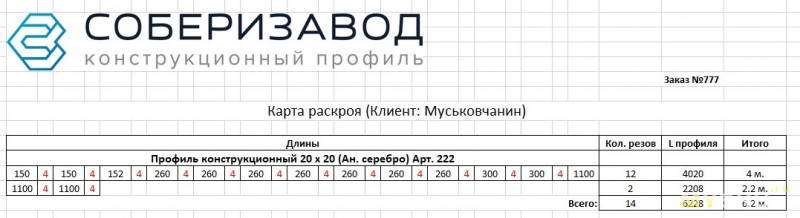
Профиль получается на 667р вместе с услугой резки.
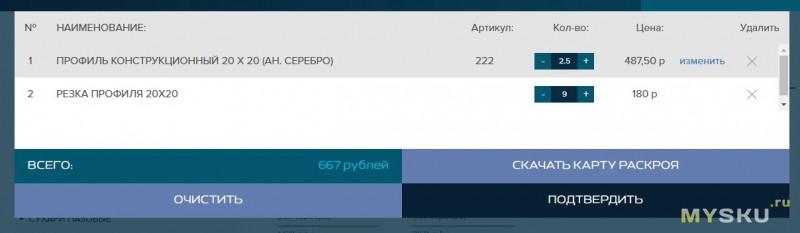
Доставка осуществляется ТК, рассчитать стоимость можно по калькулятору, так как размеры профиля вам известны, вес очень хорошо считается в карте раскроя. Для расчета нужна опция «забор груза у поставщика». Доставка Деловыми линиями обойдется дешевле, около 1000 рублей.
Можно забрать самовывозом в Москве.
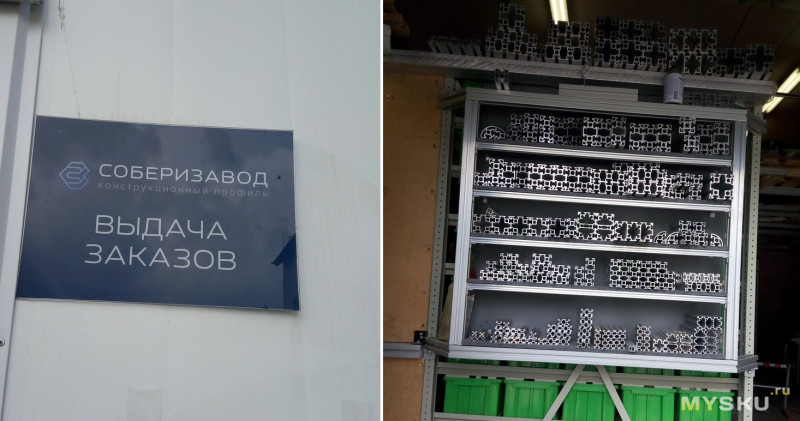
В одном месте офис, склад и мастерская, где режут профиль в размер. Есть витрина с образцами, можно подобрать профиль на месте.
Итак, начинаем собирать раму настольного станка 2418.
Вот уже порезанный профиль.
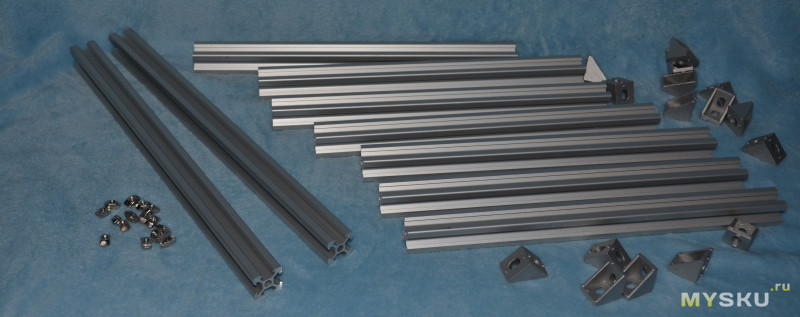
В данной конструкции я увеличил ось Z (чуть больше на пару см чем другие), чтобы использовать станок как ЧПУ сверлилку.
В оригинале ось Z самая короткая. Это уже решаете вы под свои цели. Чтобы удлинить рабочее поле, нужно купить два отрезка профиля (продольная пара) больше на нужную длину (например, +10 см), соответственно удлиняются направляющие (+10 см паре 8мм валов) и винт (+10 см винту Т8). По деньгам выходит совсем дешево озвученные +10 см: стоимость 10+10 см профиля около 40р, направляющие и винт обойдутся в плюс $6 (проверить).
Вот подготовленные для сборки уголки
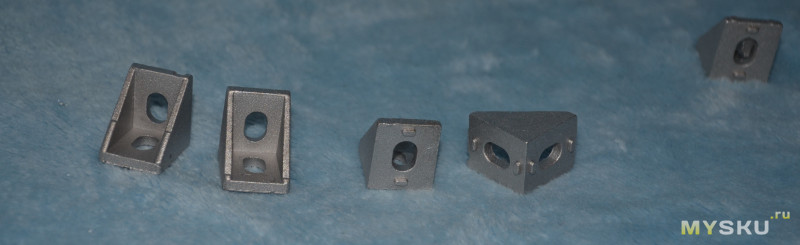
Вот таким образом следует устанавливать Т-гайки в слот. Можно не продевать с торца, а устанавливать прямо в паз профиля боком, но потом контролируйте поворот и установку гайки, так как не всегда это происходит, нужна некоторая сноровка.
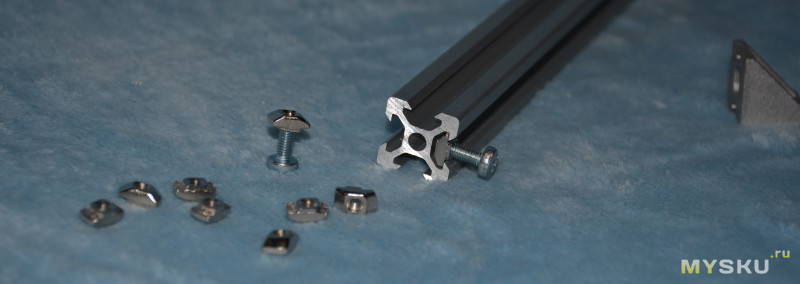
Рез профиля чистый, заусенцев нет
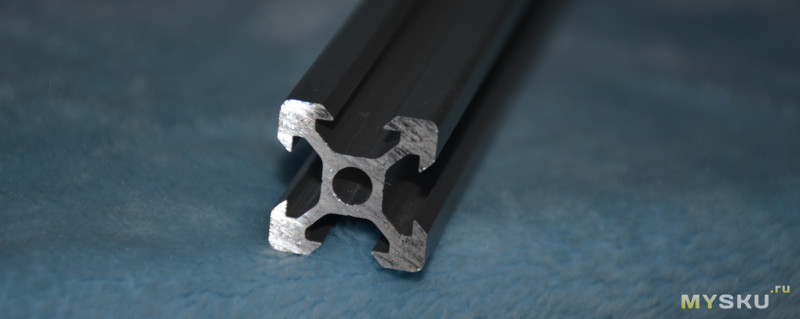
Профиль-двадцатка, то есть из серии 2020, с соответственно разменами 20мм х 20 мм, паз 6 мм.
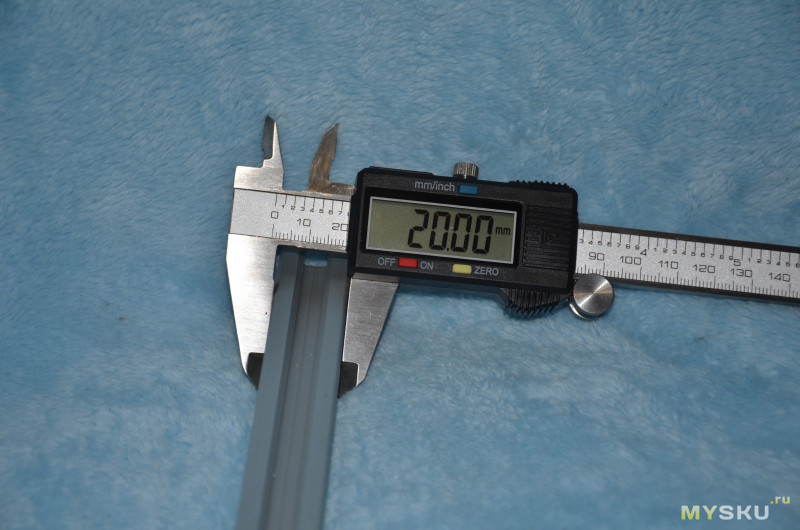
Итак, сначала собираем П образную часть рамы, крепим две продольных части профиля и одну крайнюю поперечину. Большого значения с какой стороны собирать нет, но учитывайте, что есть центральная поперечная перекладина, которая сдвинута ближе к задней части. Она является частью вертикальной плоскости, а размер смещения зависит от вылета оси Z и шпинделя. Размещают таким образом, чтобы ось вращения шпинделя была по центру станка (оси Y).
Далее собираем среднюю поперечину. Удобнее сначала установить оба уголка на отрезок профиля и зафиксировать, а затем устанавливать к раме.
Прикладываем отрезок профиля, вымеряем одинаковое расстояние линейкой, затягиваем винты. Винты нужно затягивать неторопливо, давать время Т-гайке провернуться и занять свое положение в пазу. Если не получается с первого раза, опять ослабить гайку и повторить.
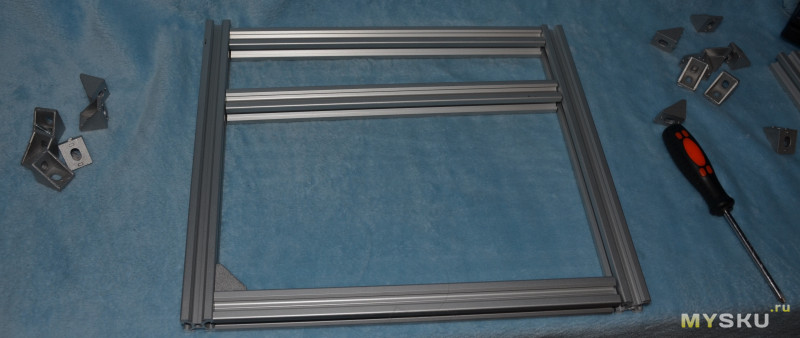
Устанавливаем последнюю часть горизонтальной рамы. Удобнее подлезать длинной отверткой. Не поленитесь и проконтролируйте прямые углы полученной конструкции угольником и диагонали — линейкой.
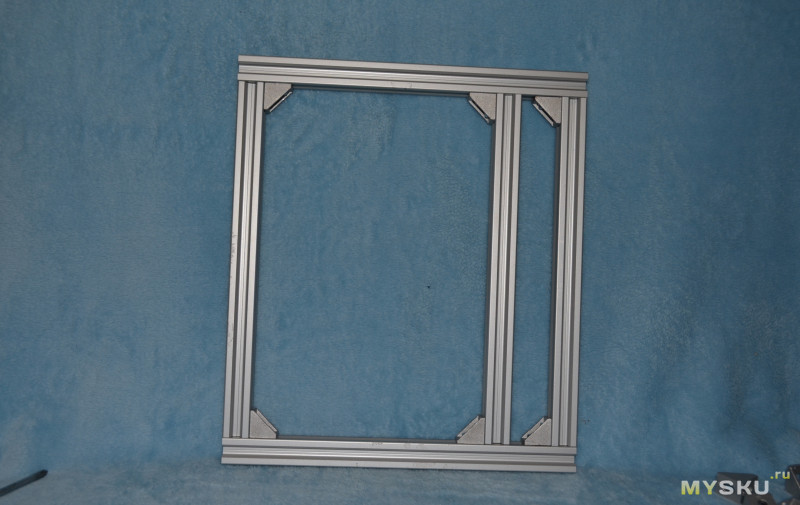
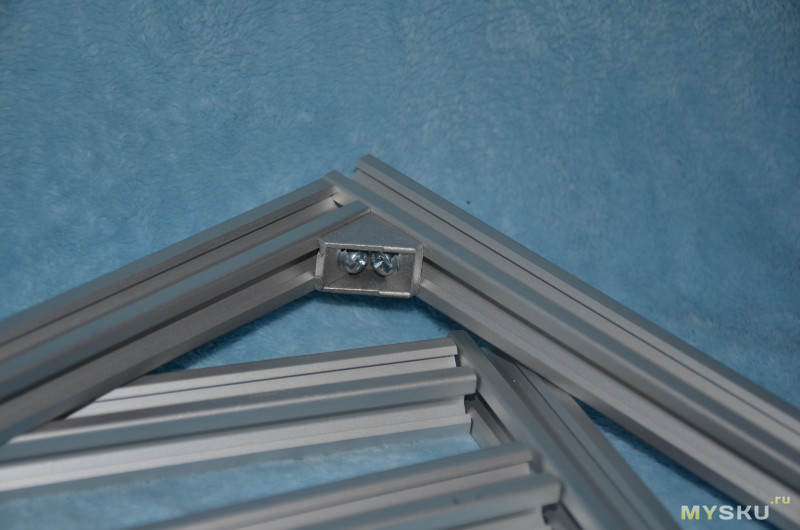
Так как уголки конструкции направлены друг к другу, то не принципиально в каком порядке собирать. Я сделал как в базовой конструкции CNC2418. Но интуиция подсказывает, что расстояние между профилями имеет смысл увеличить, особенно при большей высоте портала. Ну ладно, это можно будет сделать позже.
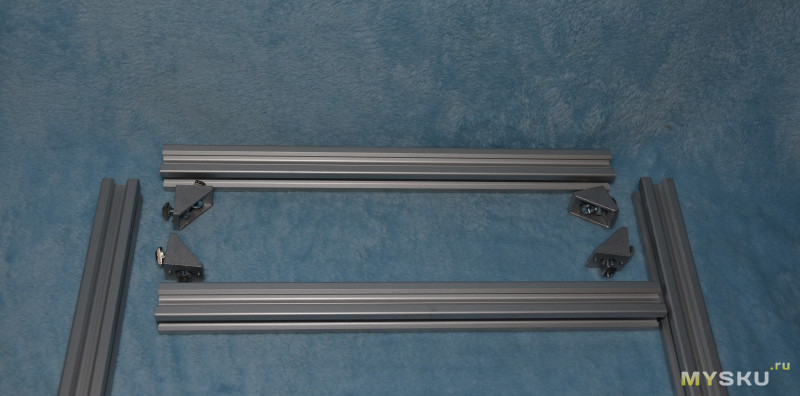
Далее начинаем собирать крепление вертикального портала
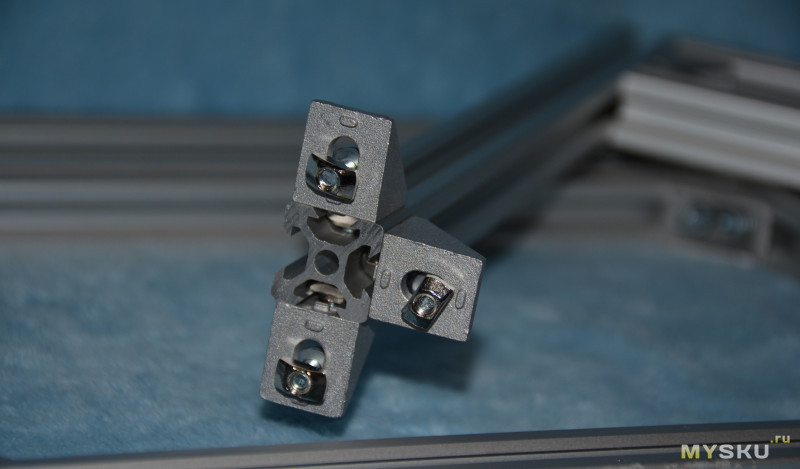
Собранный портал устанавливаем на горизонтальную часть, крепим с помощью 6 уголков (устанавливаются по направлению в три стороны от вертикального профиля).
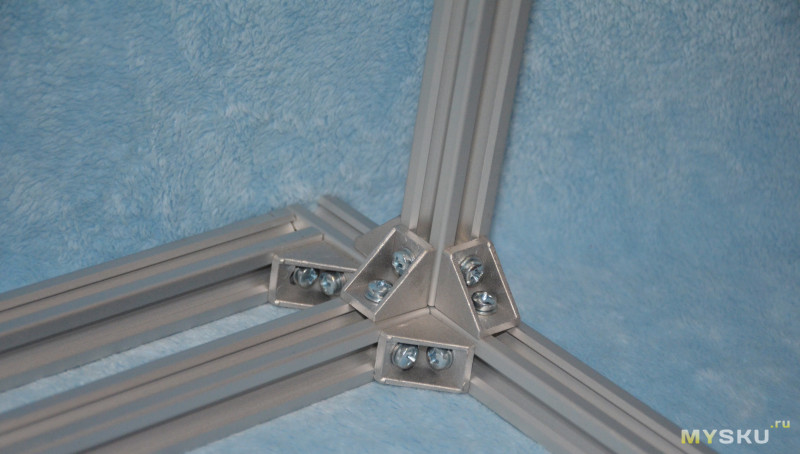
Устанавливаем, соблюдаем перпедникулярность отрезков (по угольнику). Затем по очереди затянул все винты.
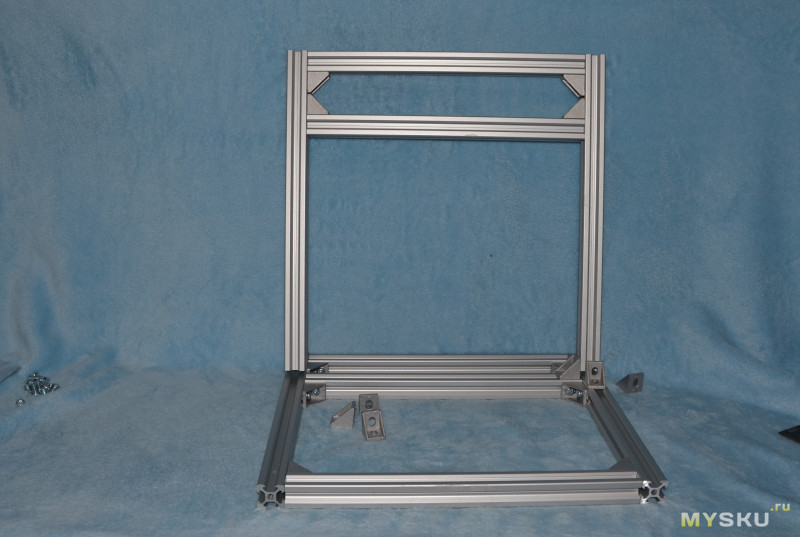
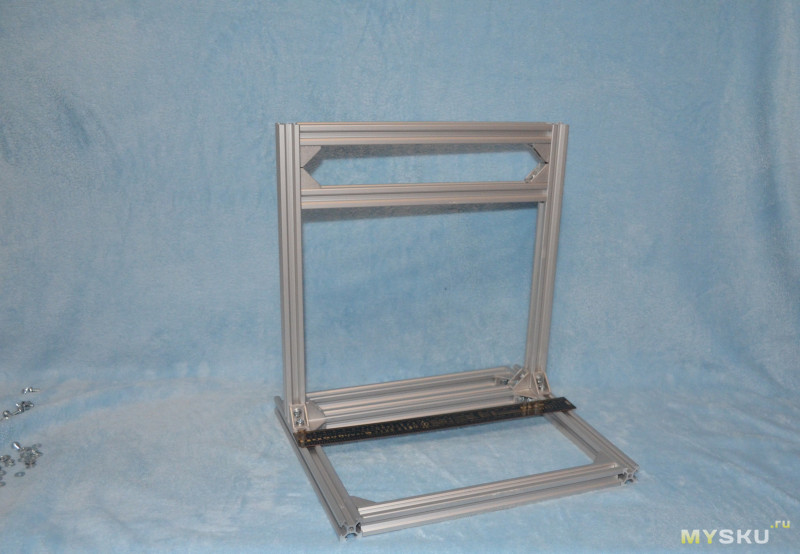
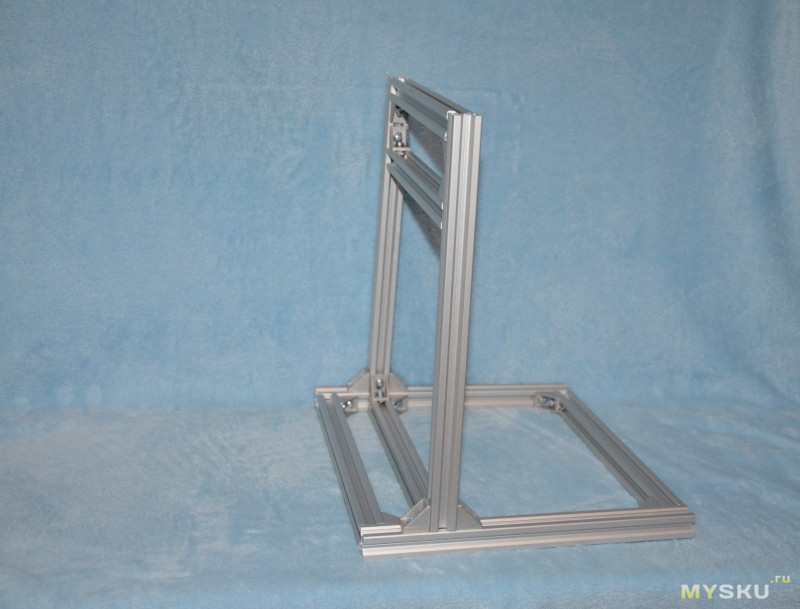
В оригинале для укрепления вертикали используется особый экструзионный уголок под 45°. Я подобный не смог найти в продаже, заменил 3Д-печатным. Ссылка на модель есть в конце топика.
Update: оказалось в оригинале 3Д печатный тоже.
Если что заменить его можно перфорированным крепежом из магазинов, либо мебельными уголками. На качестве это никак не скажется.
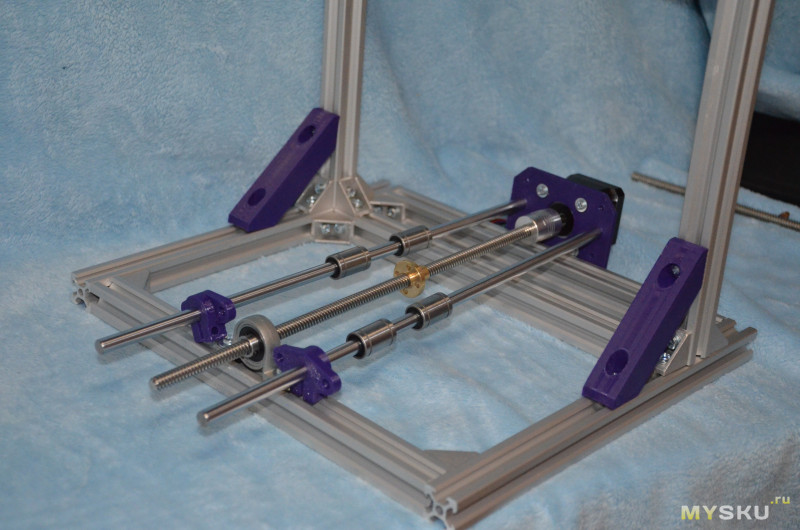
Конструкция получилась на первый взгляд прочная, не шаткая. Видно, что пластина с двигателем короче, чем связка суппортов KP08+SK8. Буду разносить пошире.
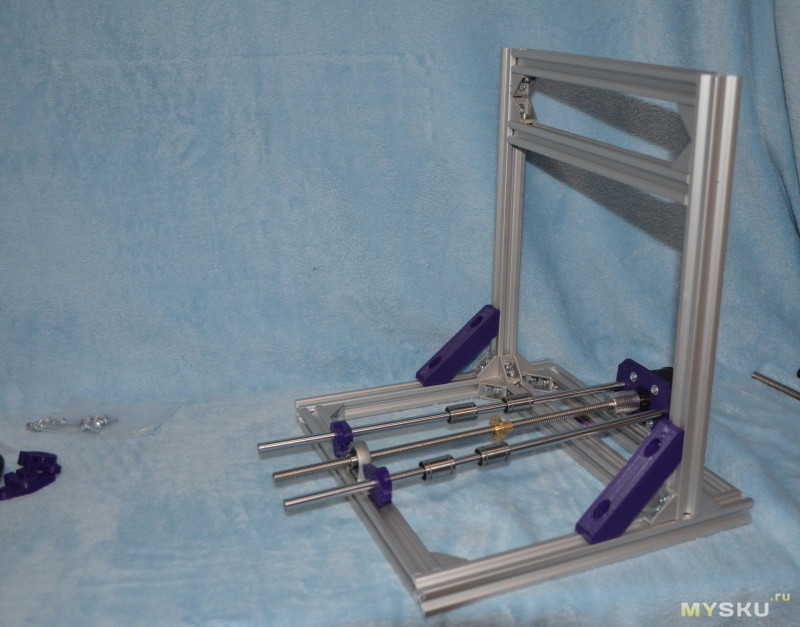
По сути данная рама является копией подобной конструкции станка CNC2418, разве что я прямо не копировал размеры, сделал чуть побольше для того, чтобы меньше обрезков от направляющих и винтов.
Сборка рамы закончена, теперь можно заняться установкой двигателей. Я использовать 3Д печатные фланцы для установки двигателей. Верхние целесообразно сделать в сборе с держателями направляющих, нижние — без держателей, так как ось Y должна быть шире. Ось Y целесообразно установить на суппорты SK8 и KP08, как в оригинальном станке. Сами суппорты можно распечатать на принтере либо купить (ссылки в конце топика, а также были в первом посте).
Для одной из осей (оси X и Y у меня одинаковой длины) взял «пристрелочный» комплект двигатель Nema17 плюс винт и суппорты. Я еще не знал своих «хотелок» на размеры станка. В итоге обрезки от винта пойдут на ось Z, нужно будет только докупить латунную гайку Т8.
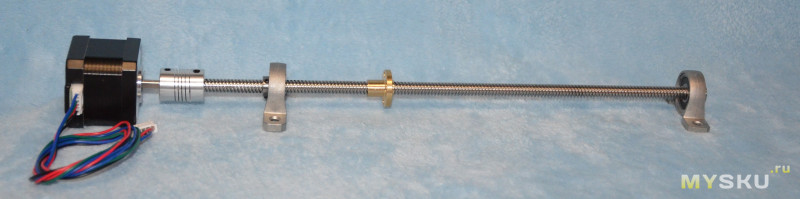
Упакован был в картонную упаковку, внутри каждая деталь в пакете отдельно
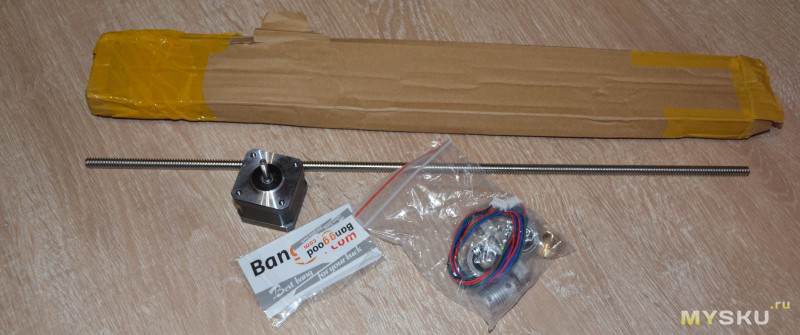
Выглядит комплект вот таким образом: двигатель с коротким проводом, ходовой винт Т8, два суппорта KP08 и две муфты 5х8.
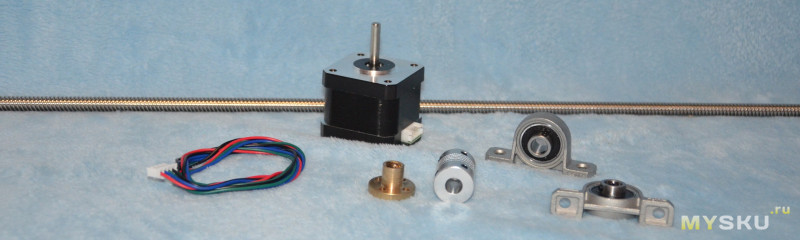
Есть аналогичный комплект 400 мм и 300 мм, а также без двигателя на 600 мм (с суппортами и гайкой).
Если брать без большого запаса, то вариант на 400 мм, хорошо пойдет для «увеличенной версии» станка
Дополнительная информация - фото комплекта по отдельности
Маркировка двигателя RB Step Motor 42SHDC3025-24B-500, посадочное место Nema17
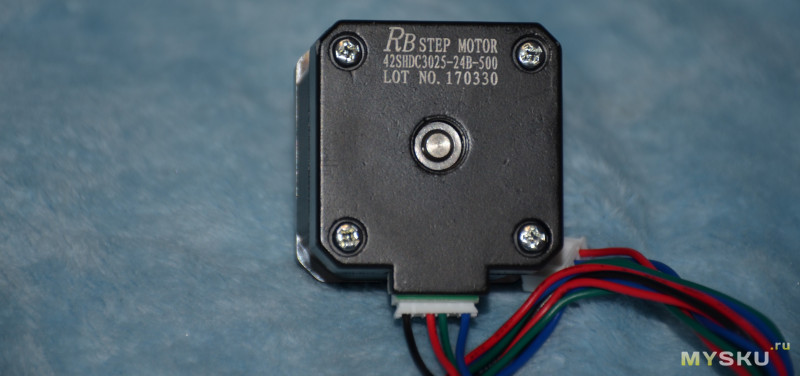
В комплекте короткий провод для подключения. Удобно, можно просто нарастить длину, не трогая разъемы.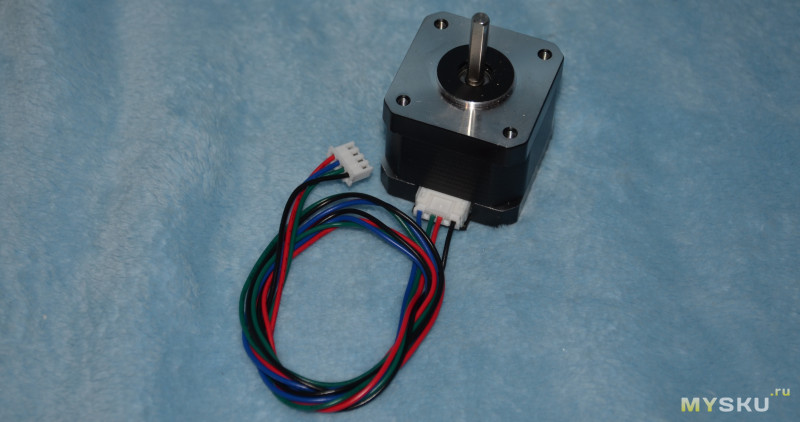
Винт Т8, гайка
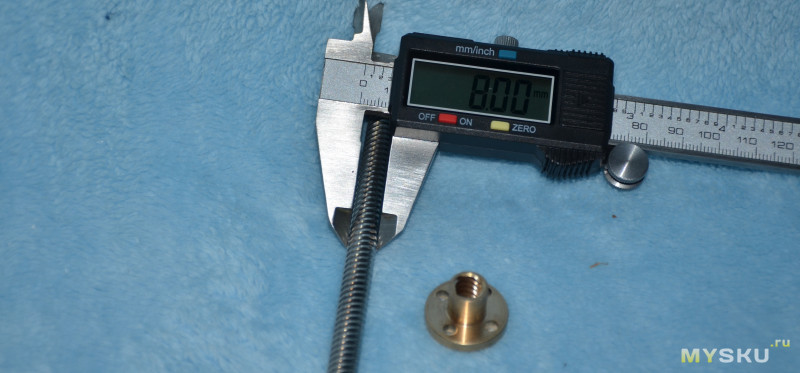
Суппорты КР08.
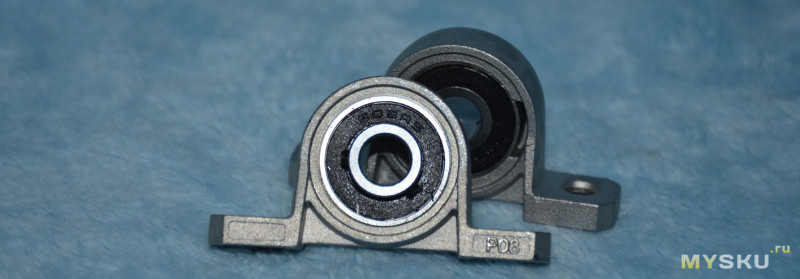
Удобно крепить на профиль. Если используется широкий фланец для установки — то лучше использовать версию суппорта KFL08, она позволяет крепить винт не на профиль, а на фланец.
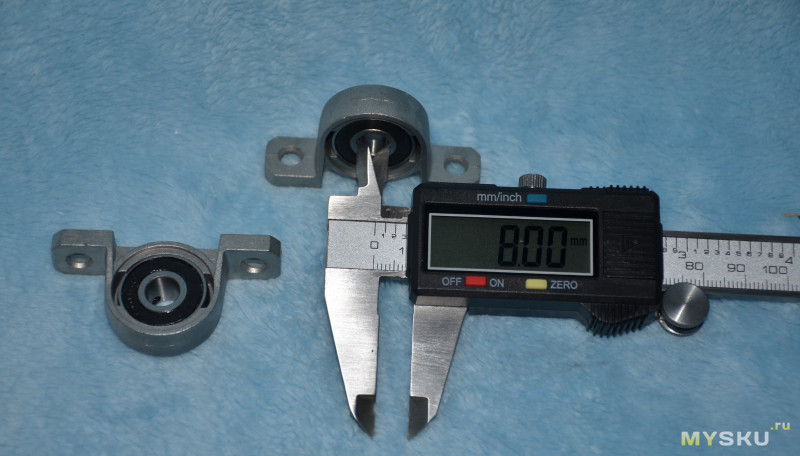
Муфта 5х8 — разрезная муфта для подключения вала двигателя к винту.
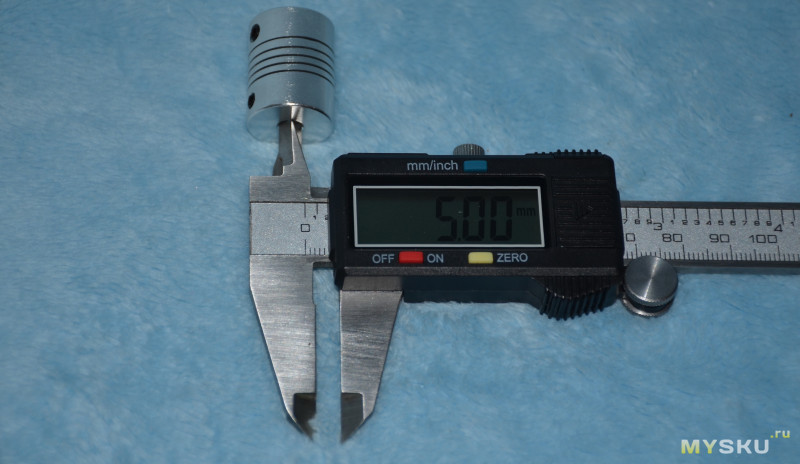
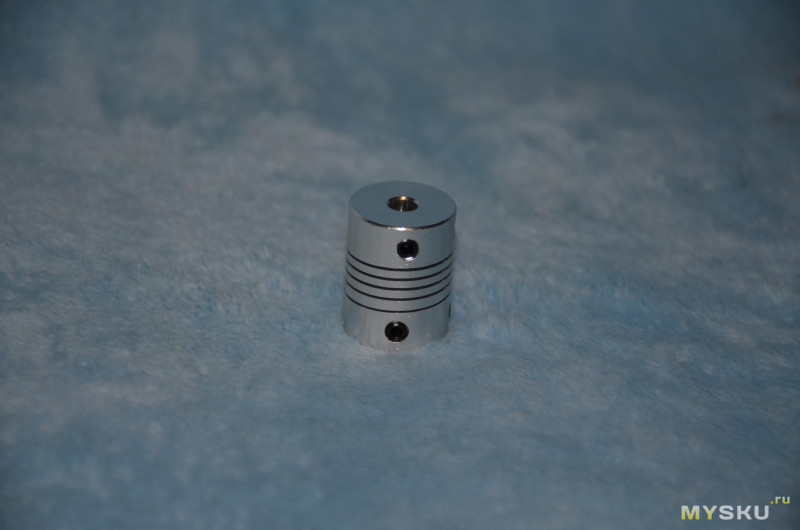
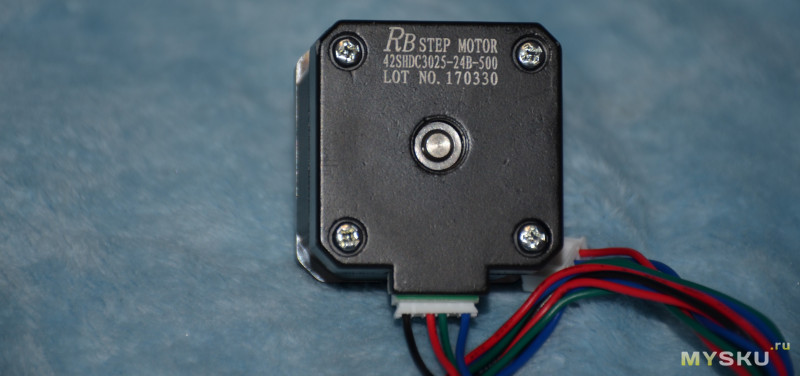
В комплекте короткий провод для подключения. Удобно, можно просто нарастить длину, не трогая разъемы.
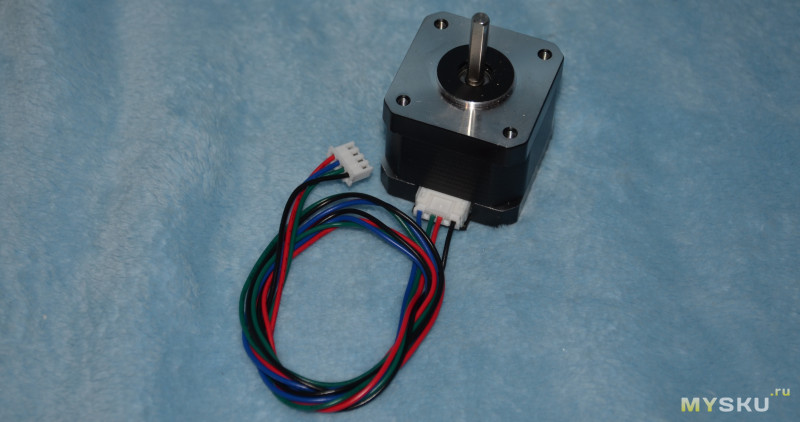
Винт Т8, гайка
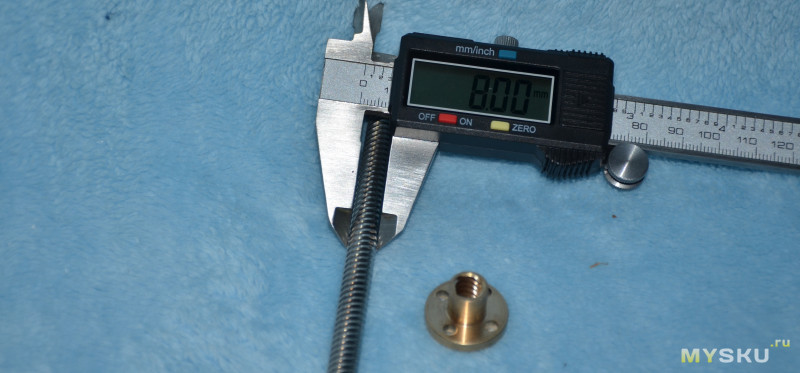
Суппорты КР08.
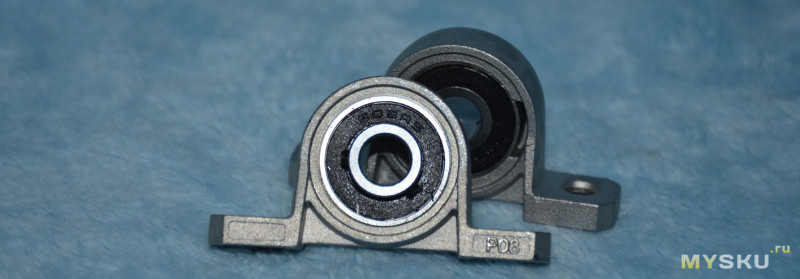
Удобно крепить на профиль. Если используется широкий фланец для установки — то лучше использовать версию суппорта KFL08, она позволяет крепить винт не на профиль, а на фланец.
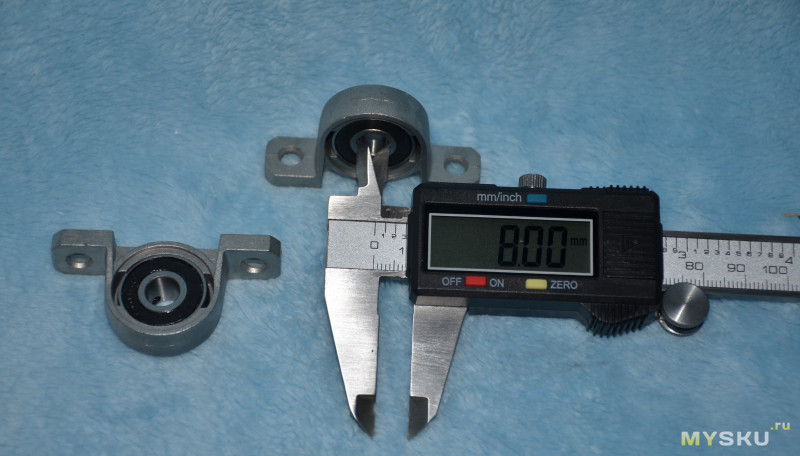
Муфта 5х8 — разрезная муфта для подключения вала двигателя к винту.
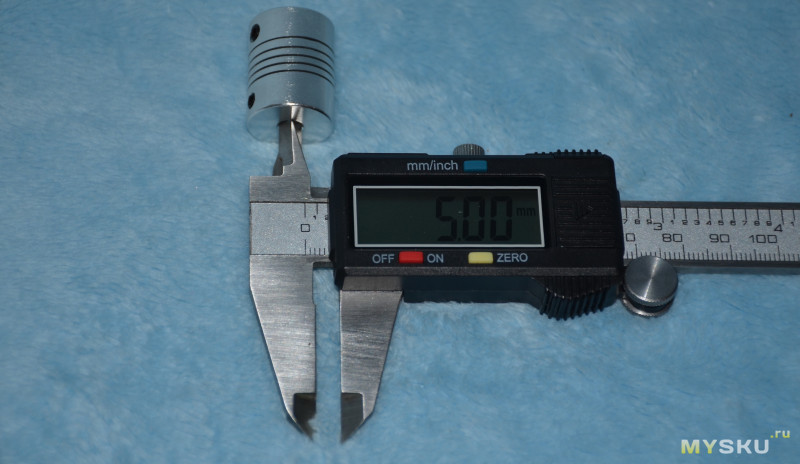
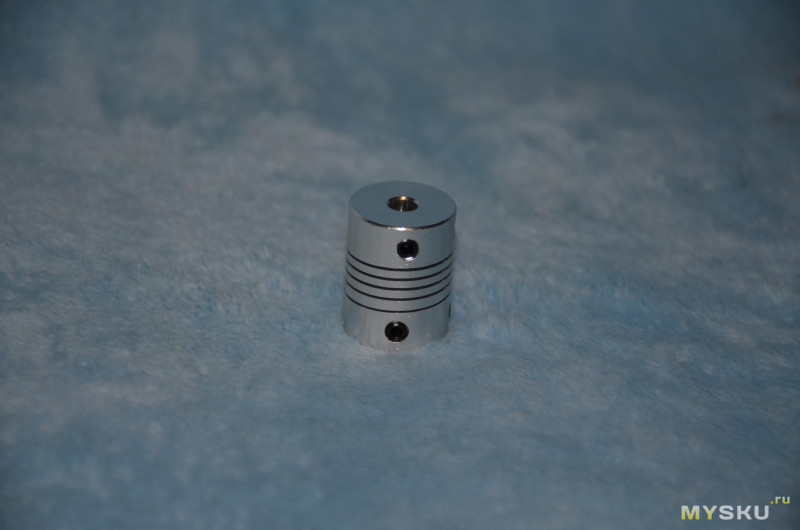
Вот как крепится двигатель в оригинале на ось Х. На небольшую алюминиевую пластину.
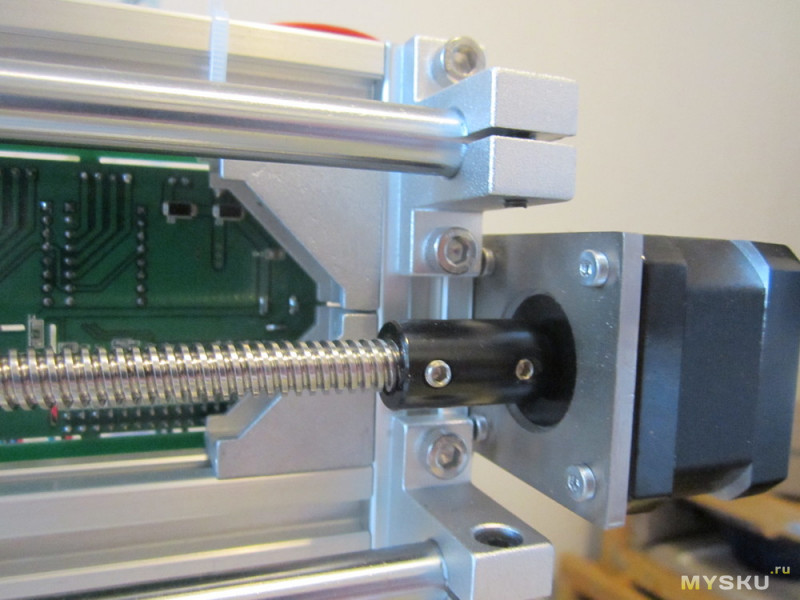
Сделал тоже самое, только с печатной пластиной. Заодно будет суппортом для направляющих.
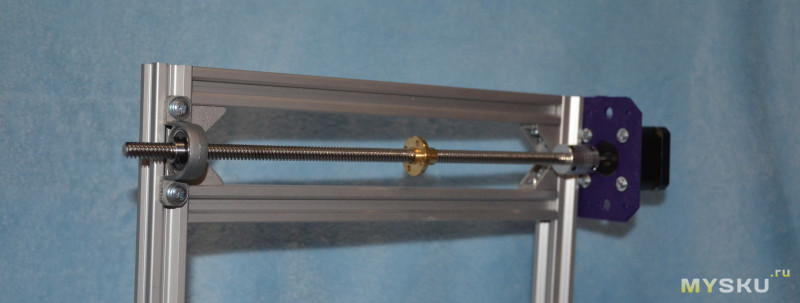
Лишнюю длину винта уже отрезал для оси Z (ось Z в процессе пока, информация будет отдельно, скорее всего также 3д печатная).
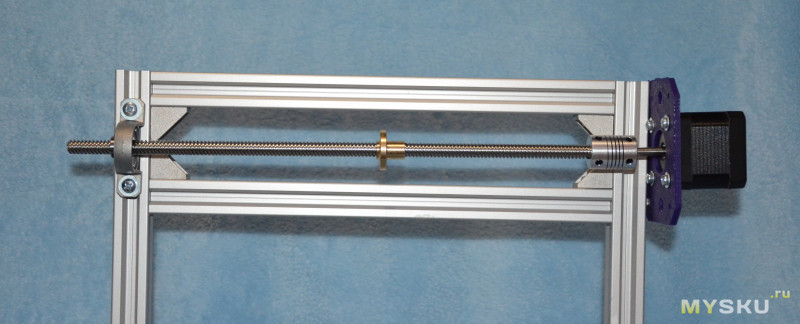
С большой вероятностью нужно будет удлинить провода двигателей, чтобы аккуратно проложить его по профилю в верхнюю часть до платы электроники (скорее всего будет CNC Shield). Да и не мешало бы установить концевики крайних положений.
Основная информация по сборке уже есть, можно приступать к оценке затрат))))
Калькуляция
Теперь, по просьбам в комментариях в первой части, я предлагаю обсудить калькуляцию затрат. Естественно, я потратил меньше указанного, так как двигатели и большая часть комплектующих у меня была в наличии. Сильно дешевле будет, если использовать самодельные печатные уголки для профиля, суппорты, фланцы и так далее. На работу станка по сверлению печатных плат и по фрезеровке мягких материалов это вряд ли скажется. Еще хороший вариант — использование перфорированных пластин из строительных/хозмагов. Пойдет для усиления углов, в том числе вертикального и для установки двигателя, при условии высверливания центральной части под вал. В место перфорированного крепежа можно использовать самодельные из алюминиевого листа или фанеры.
Однозначно нужно приобретать профиль 2020, иначе это будет станок совершенно другого типа. Можно сделать тоже самое из алюминиевого уголка или прямоугольной трубы, но только из любви к искусству))) Есть более оптимальные конструции в плане жесткости для сборки из уголка/трубы.
Однозначно к профилю нужны Т-гайки. Можно купить Т-болты, но Т-гайки более универсальные (так как длину винта можно применить любую).
А вот остальное можно менять на свое усмотрение, можно даже вместо ходового винта Т8 использовать шпильку из нержавейки. Разве что количество шагов на мм пересчитать придется в прошивке.
Двигатели можно снять со старых устройств/оргтехники и планировать посадочные места уже под конкретный тип.
Электроника практически любая (Anduino UNO/Anduino Nano, CNCShield, Mega R3+Ramps, драйверы A4988/DRV8825, можно использовать плату-переходник под Mach3 и драйверы TB6600. Но выбор электроники ограничивает используемый софт.
Для сверлилки можно использовать любой двигатель постоянного тока, который позволяет установить цанговый патрон и имеет приличные обороты. В базовом варианте присутствует высокооборотистый двигатель 775. Для фрезеровки можно использовать б/к шпиндели ватт на 300 с цангой ER11, но это сильно удорожает станок в целом.
Примерная калькуляция затрат:
профиль Соберизавод 2020 (2,5 метра) = 667р
профиль Соберизавод 2080 (0,5 метра) на рабочий стол = 485 р
Два комплекта для осей по 300 мм 2х$25
Уголки для профиля 16 шт. Лот на 20 шт выходит $5.5 с доставкой
Т-гайки примерно 4р/штука если брать большой пакет. Нужно не менее 50 шт (крепление двигателей, суппортов). Винты к ним не считаю, обычно несколько копеек/штука в зависимости от качества. Итого около 400...500р.
Двигатели Nema17 3 шт $8.25 каждый
Электроника CNC Shield board $2
Arduino Uno $3.5
A4988 три штуки по $1
Станок выходит около $111. Если добавить шпиндель:
Двигатель 775 $9
Патрон ER11 $7.78,
то итог стоимости около $128
3Д печатные детали не оцениваю. Можно заменить перфорированными пластинами/уголками из крепмаркета и подобных магазинов. Провода, изоленту, затраченное время также не оцениваю.
Напомню, что не во всех вариантах комплектаций CNC2418 есть такие хорошие 775 двигатели и, тем более, цанга ER11.
Варианты подешевле:
Вал 8х600 пару шт и распилить пополам. Для Z-оси взять короткий 8х300
Вместо SC8UU использовать LM8UU
Суппорты SK8, KP08, держатели Т8 гайки, держатели подшипников LM8UU, уголки для профиля — 3д печатные.
Можно взять направляющие большей длины, чем в Китае, например в магазине Duxe.ru. Как вариант, можно купить Вал полированный SFC-8/600 и SFC-8/1000. Цена вопроса 250 р и 410 р соответственно (плюс доставка). Из этого получится три пары направляющих с большим запасом.
Инструкция по сборке оригинального 2418
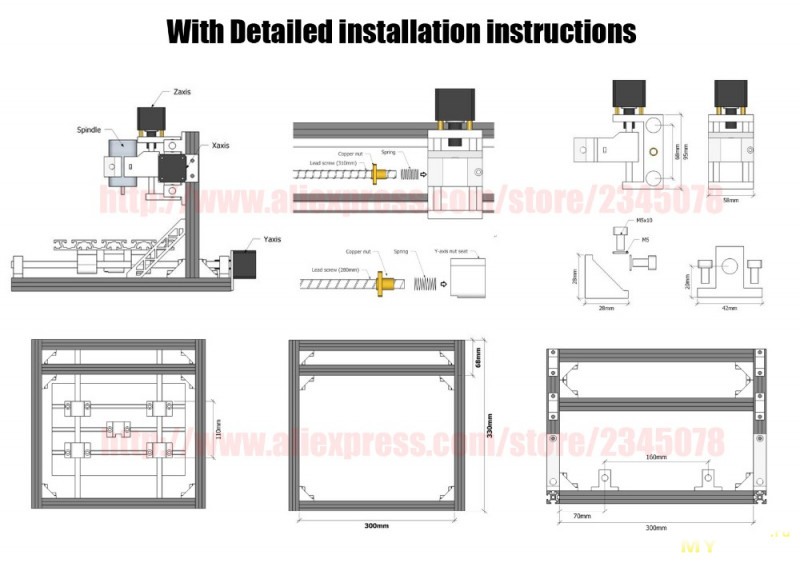
3D печатные запчасти, для экономии:
Целиком проект CNC с печатными деталями. Рекомендую воспользоваться моделью кареток XY отсюда
Модель крепления для шпинделя
Похожий зажим от CNC3020
Хорошее крепление пары LM8UU
Простой держатель LM8UU и еще один
Подшипники lm8uu можно также распечатать из PLA
Nema 17 motor mount — крепление мотора
Суппорт 8 мм c подшипником
SK8 mount
SHF8
Усиленный уголок для профиля
Еще несколько деталей, в том числе фланцы и уголок под 45°
Спасибо за ваше внимание. Далее будет про сборку осей XY и электронику
Самые обсуждаемые обзоры
+81 |
4481
156
|
+85 |
3266
85
|
+215 |
3775
36
|
По деньгам получается выгоднее собрать станок 30х20 или даже 30х40, будет чуть дороже по профилю и по направляющим, основное (уголки и прочая крепежка, двигатели, шпиндель с цангой) будет тоже самое, и цена вырастет не сильно. Правда кроме поля возможности по обработки тоже не вырастут. жестче он не станет.
почему б не использовать такие штуки?
alumica.ru/accessories/zhestkost/g206060
alumica.ru/accessories/zhestkost/t206060
Мне кажется жесткость конструкции от этого только выиграет. Поданным ссылкам они из 3 мм стали их хрен согнешь. А те уголки на которые предлагается собирать, я так понимаю они из цинка и довольно пластичные.
Да и одной Т образной косынкой можно было б заменить 2 уголка и упор из АБС, что как бы капельку но снизит цену при увеличении жесткости.
Мои уголки из какого-то порошкового сплава, самые дешевые
Спасибо за ссылку!
С китайскими профлями и фурнитурой дел не имел, у них крепление на м3 м4 в сухарь/закладную гайку происходит?
И нужно будет обеспечить постоянный и солидный прижим, чтобы этот зазор не сказывался. А ведь конструкция вибрирует… Плюс зазор в балке под Т-гайку и болт.
Другое дело если сварить пластину и балки. Тогда да, пластина выигрывает.
а кто мншает затянуть хорошо? если напрягает вибрация, то вместе с анаэробом. проблема надумана, как мне кажется.
Хотя для такого станка и не слишком точные уголки с головой пойдут :)
если изначально делать криво, то это будет кривой станок в квадрате ;)
Да, и не ваши ли это слова:
Вы уж определитесь как-нибудь. «С головой пойдут» или «без головы». ))
далее для жесткости предложена деталь из абс. как бы упругость стали и абс сравнивать не будем?))
А что всякого г… на рынке много, так кто ж спорит?
Вот что надо брать.
www.rsi-llc.ru/catalog/73/362/
По малолетству имел дело с рамами на косынках. Если косынки не подварить — туфта. Зажимай-не зажимай. Мы же все таки раму для фрезера пытаемся сделать, а не стол на дачу. Но каждый выбирает, конечно, сам.
Скорее всего так и будет, skeptik. Вместо 3Д печатного уголка на 45° установить подобную пластину. надо только найти подешевле.
Если брать вместе с профилем — у Соберизавода:
пластина 60*60 44р
пластина 60*80 49р
Т-образные пластины 39р
Только лучше брать все сразу с профилем, я то упустил момент, мне поехать только за пластинами не резон.
1-2 уголка только этих все же надо, чтобы стягивать балки и угол между ними держать. Прихватил, снял уголки, перешел к следующему сочленению.
Это уже давно является аксиомой — сварные и литые конструкции без отпуска со временем уйдут от первоначальной геометрии :)
Конечно без тепловой обработки не обойтись.
варил раму из 25ой профильной трубы с толщиной стенки 2мм
www.rsi-llc.ru/catalog/73/362/
Китайцы, не дураки. При их стремлении все удешевить, они давно бы использовали косынки. Подумайте над этим.
хотя, косынка самая мелкая(напомню у на с она стальная 3 мм толщиной) для 20профиля весит как полметра профиля. разорятся китайцы на доставке))
Сомнение берет в этом материале.
Делается под фрезу и лазер 5 Вт, с переключением.
Голова по Z и каретка по Х — не люфтят со втулками?
Вот китайцы, проще самому собрать ))))
Время на ожидание, подгонку и сборку не учтено, двигатель + цанга нет, платы для драйверов нет,
а уж вертикальная ось — там вообще в сборе идет, я бы вручную так качественно не сделал. Там подшипники вплавлены что-ли в напечатанные детали.
Лучше купить за 228 $ и голову не морочить, хотя у продавца еще есть с лазером на 5 вт интересный вариант, но чуть дороже.
https://aliexpress.com/item/item/2016-New-GRBL-CNC-machine-3-Axis-Pcb-Milling-Machine-2418-Diy-Wood-Carving-Mini-Engraving/32704119622.html
Остальное сильно дороже ($250+)
По моим подсчетам $128 c цангой.
3Д печатная ось мне мало нравится, подшипники не вплавлены, там или втулки или или lm8uu внутри, их просто не видно.
А время на постройку и доводку вообще тяжело оценить.
Покупной 2418 или 1610 тоже из коробки редко работает как надо.
Посмотрите выше комментарий wallie, сколько всего сделано. Да и на форумах часто сообщения про настройку 2418… Недавно был обзор кстати про покупку 2418
Цанга ER11 есть у этого продавца и отдельно и в наборе фрезера. На момент покупки был с доплатой +7$. Цены зависят от мощности лазера: 228$ без лазера, 310$ с 5,5 вт лазером. Мне лазер не нужен у меня ребенку 8 лет, еще без глаз останется.
Все собралось не с первого раза конечно, оси там пришлось менять местами, они чуть по длине отличаются, но можно было не менять. Заработало с первого раза, никаких косяков и люфтов, все идеально.
Еще заметил, в калькуляции нет стоимости стола, а там специфический профиль цельным куском.
Кстати отзывов там русскоговорящих наверное 80% из 621. Почти все в 5*, на 3* и ниже всего 7.
Управляющая программа mach3 для станка (у меня LPT).
(который крайне не рекомендую покупать никому там ремни). Так работал довольно долго и ругался что станок кривой.
Потом наткнулся на видео которое пролежало в закладках месяцев 6 но я его таки посмотрел и начал работать в Fusion360
У того видео есть продолжение с более развёрнутыми пояснениями.
В общем сейчас сразу рекомендую не тратить время на Easel и сразу начинать с Fusion360 так как это очень мощный и простой инструмент. И главное алгоритмы работы с CNC.
А Вы печатные платы не пытались на Вашем станке фрезеровать? Я себе станочек подбираю под печатные платы… В принципе и небольшие доработки станка не пугают, но хоть убедиться заранее, что потенциально такое применение возможно.
И не могли бы Вы выложить фото готовых работ этого станка, особенно с тонкими и мелкими деталями?
www.youtube.com/results?search_query=2418
Вот когда оплатил, уже увидел, как платки делают на 3D принтере печатая тонкий слой пластика в тех местах, где будут дорожки. Мне кажется, это более перспективно.
Сейчас в конце лета хочу начать собирать полноцветный 3D принтер (с головкой даймонд и трехцветной подачей пластика), только будет куб и из аллюминиевых прямоугольных профилей и 608zz подшипников качения (думаю, жесткость будет, что может добавить скорости печати).
данный фрезер в таком виде в котором он приходит из китая, разумеется не способен на такой подвиг :)
но если его довести до ума, думаю вполне возможно
Поэтому я плюнул на минимализацию там, где она не слишком нужна и делаю дорожки 0.4 с интервалом по возможности 0.5, но можно и меньше.
А на более тонкие дорожки с меньшим шагом перехожу уже непосредственно перед теми компонентами, где это требуется.
Хотя и подозреваю, что может раньше проблема была не только в толщине дорожек, но и в недостаточном опыте.
Сейчас я вот текстолит обязательно шкуркой полирую перед ЛУТ и ацетоном обезжириваю, и с лупой обязательно после счистки бумаги прохожу и зубочисткой дочищаю, и при переносе тонера силиконовый коврик подкладываю, чтобы прижим был равномерный — а раньше так не делал, вот может и отходили дорожки…
Но как первый станок, для ознакомления, самое оно. Ввиду его цены. А может кому и этого будет достаточно.
иметь жесткую конструкцию
не иметь сильных люфтов
шпиндель должен обеспечивать обороты от 15000
шпиндель не должен иметь сильное биение
вряд ли удастся это чудо довести до кондиции, чтобы на выходе иметь годный результат, лучше присмотритесь к станочкам марки «вектроник»
С такой конструкцией вас еще не знакомил.
Предполагается кроме основного подвешивать её на вертикальные плоскости, типа дверей, мебельных элементах, чтобы как то её оживить, нанести те же узоры и т.д. А то глаз не радует, своей скучностью.
А вообще кто не хочет идти по следам китайцев смотрим ещё кучу проектов здесь i4.ru/index.php/board,114.0.html
для 3дпринтера сойдет, в качестве фрезера я бы такую конструкцию не стал собирать
С синхронизацией тоже вроде проблем никогда не было. Долго всё рассказывать.
Уже пройденный опыт. Подробно на различных форумах разжевано.
Вот один из станков большого формата, там по оси Х стояли 2 ШД.
Как в этом обзоре собираются ставить.
Что то они мне не сильно внушают доверия.
Я с такими пока не экспериментировал.
Интересно глянуть как себя поведут, ну и по линейным самопальным, выше вопрос задал.
Что то мужики вы немного намудрили. ;)
Я свой наоборот ужесточал, да и движки все же Нема 23 ставил.
Да и ту же ось Z усиливал, вот так
ставим на нее небольшой XY модуль, например бушный японский THK, на Z такой же готовый модуль
имеем весьма жесткую конструкцию, а самое главное с качественной механикой, способной грызть даже цветмет
Я лично для дома небольшую, легкую и более менее по дизайну чтобы дома вписывалось.
Также быстро убрал, достал и т.д.
Ну и по бюджету чтобы не ударяла.
Для тех же элекронщиков. Рисовать платки лайнерами, потом сверловка отверстий.
Там не много мусора. Лазер, гравировка, выжигалка и т.д.
Что то мелкое по дому. Типа перифирии к компу или планшету.
впрочем… у всех свои приоритеты:)
Ну и дребезг металла меньше. Фанера не такой резонатор.
У меня даже был проект, с узорными боковушками. ;)
Топорные формы, раз мы ЧПУ имеем напрягают.
Всё должно быть красиво и глаз радовать.
Боковушкам я даже отдельно тему посвящал. Разного профиля.
Например.
Ну и быстро что нашел.
У нас народ, тысячами просеивался по различным параметрам.
Вот когда хоть что то. было толковое в человеке, то он получал доступ на Мастеровой master.i4.ru/ Там заметьте мало народу, а зато тем больше чем на i4.ru/ Сокровищница так сказать. Много очень интересного, профан навряд ли поймет. Годами копили.
к тому же, из за слабой жесткости конструкции станка при фрезеровке фрезу будет так колбасить и вы получите такой шум, что мало не покажется.
деревяшечные конструкции годятся только для того, чтобы изучить работу ЧПУ, мое имхо.
Самолеты и то до сих пор на ней делают.;)
Не видел, чтобы пилоты из кабины выбрасывались из за резонанса.
MDF кажется лишена такого недостатка но обрабатывать её та ещё проблема особенно на CNC.
Попробовал понравилось.
Итальянцы из фанеры промышленные станки делают, на очень дорогой комплектации.
Они по вашему дураки?
«А на заре развития авиации некоторые авиационные двигатели вызывали столь сильные резонансные колебания элементов самолета, что он полностью разрушался в воздухе. „
Я вот чётко понял что если станок должен стоят дома то он обязательно должен быть закрыт в пыле звуко защитный кожух а не красоваться своим дизайном. Кожух да, можно и награвировать что-то.
Да и в гараже тоже кожух из картона просто заруливает не закрытый станок. Пылища не разлетается по всему гаражу, шума меньше когда там находишься.
Кстати над пылеудалением тоже работаем. Тихий домашний вариант, под малую пыль.
Ладно мужики, языком чесать и придумывать какие то страхи можно долго.
Глаза бояться. да руки делают.
Пойду еще одно ноу хау опробую.
Дерево фрезерую из за чего много пыли. В последнее время кроме основного проекта под который покупался станок делаю всякую фигню почти каждый день. Ну а чего станок то есть) Для ребёнка тоже фигурки вырезать всякие хорошо.
Подскажите, пожалуйста, — как правильно называется деталь для вертикальной подачи фрезы?
фрезеры по металлу, которые с ручным приводом? под переделку на ЧПУ они мало пригодны, там направляющие типа «ласточкин хвост», ресурс для ЧПУ очень не большой, а под рельсы с ШВП переделывать — нужны станки, к которым не у всех есть доступ, да и по цене будет наверняка дороже.
Также предложение к автору в будущих частях, хотя бы теоретически, осветить вопрос/возможность «преобразования» в 3D-принтер. Возможно ли, какие доработки для экструдера, держателя катушки и т.п. Особенно подогреваемого стола, тем более самодельного, т.к. стандартных для такой «кинематики» нет.
Если я правильно понял, у автора есть свой 3D принтер и его замечания (мнения) будут особенно ценны.
ЗЫ. Я, в первую очередь, «про это» — «Ось Z — 45 мм». Не интересно для 3D. Т.е. либо переделывать всю «ось Z», либо делать в виде съемного модуля.
Ну и подогрев для увеличения номенклатуры используемого пластика.
Гравер должен быть мощным, и не обязательно быстрым. А вот 3D принтер — быстрым и точным, но при этом он практически не нагружен — т.е. жесткость рамы может быть гораздо меньше.
На практике это приводит к тому, что используются разные приводы — гравер таскают винтами, а 3D принтер — чаще ремнями.
И да, разная конструкция оси Z, стола.
А потом что было, то и полюбила.
Алена Апина ©
Подскажите, какой у Вас 3D принтер???
в предыдущей статье была такая фраза:
Сводную табличку пожалуйста со ВСЕЙ комплектацией и актуальными ценами! Иначе это просто голословные утверждения.
Даже прикинуть на пальцах:
Стол -1150р
Профиль -700р.
Z голова со шпинделем, ШД, винтом, направляющими и прочей печатной лабудой -3350р (или есть где бесплатно распечатать?)
ER11 -500р
+ 2 ШД -900р.
4 вала 8мм*350мм -1050р
2 винта 8мм*350мм + разрезая гайка -800р
8 держателей валов -400р
Плата управления/драйверы -1250
БП 24В 6А -1000р
Итого, по таким беглым прикидкам вышло:
11.100 РУБ! / 57 = 195 $
плюс крепеж, кронштейны для ШД, зажимчики для заготовок, овнофрезы, муфты, провода.
5Вт-ный лазер тоже самому собрать? Чтобы уж точно с 300$ конкурировать.
И… самое интересное! Смотрим по ссылкам в начале Вашей же предыдущей статьи, цены от 11.100 до 11.350р в комплектации которую я накидал за 15минут.
Так что пытаться сэкономить на наборе, который китайцы вылизали донельзя (из-за довольно большой конкуренции на рынке) ни к чему не приведет. И если уж собирать что-то самостоятельно, так что-то стоящее и умеющее справляться с мягким цветметом, хотя и там у китайцев есть что предложить.
Кстати, если собирать станок самому, то нужно иметь представление что такое ЧПУ, и тут 2418 отличное наглядное пособие для обучения азам.
Остался один вопрос. В стандартном и исполнении указан ход оси Z 45мм при высоте станка 240мм. Автор же увеличивает корпус до 300мм (+60мм), но при этом ссылка на eBay напечатанного комплекта с кронштейном оси Z та же что и у базового 2418 (45мм).
Я так понимаю что нужно брать другой кронштейн мотора для оси Z.
И судя по отзыву на eBay комплект тот кривой. По этому надо искать чертёж этого комплекта для печати (если кто даст ссылку скажу преогромное спасибо)
В общем если коротко и сухо то вопрос, как рассчитать вертикальный размер корпуса относительно параметров оси Z. Гуглил, не нашёл ответа.